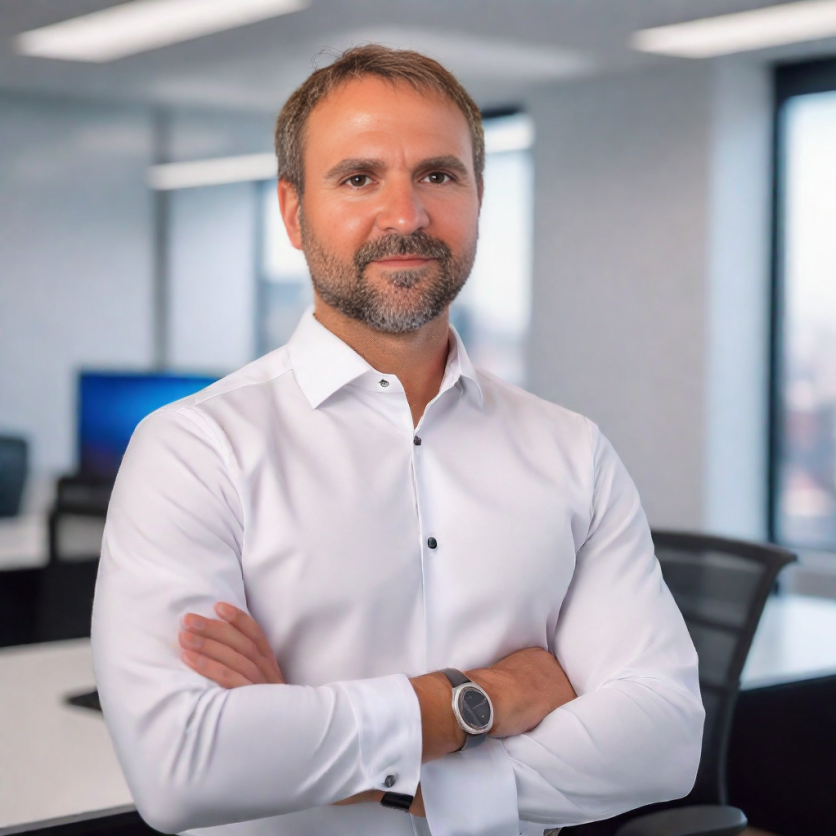
From finance to fashion merchandising, companies all around the world are going green—and the construction industry is no exception. Green building is taking the industry by storm, but Graceful Management Systems (GMS) co-founder and CEO Tommy Stanek knows that there is more to green building than choosing the right materials and sustainable transportation methods. For decades, the construction industry has had a problem with waste, but the artificial intelligence behind the Graceful Management System is offering a more eco-friendly future for this top-performing industry.
Construction teams can't make something out of nothing, which is why this niche is known for high dollar spending on materials. From wood and concrete to cabinets and countertops, construction teams rely on piecing together materials to create their final products. Unfortunately, the reality is that a good amount of these materials actually go to waste for construction projects. Up to 30% of all construction materials ultimately find themselves in landfills due to estimation errors, installer errors, and poor waste disposal practices, making the construction industry a high contributor to global waste.
This reality is bad for the environment, causes unnecessary project costs, and damages a company's reputation. To help mitigate these impacts, construction teams must become more adept at planning and purchasing. Graceful Management Systems, a small Midwest startup that has raised over $1 million to address major construction problems related to resource management, has harnessed the power of artificial intelligence to bring the construction industry into a new era of low-waste sustainability.
"Material waste is a major area of loss for construction companies," explains CEO Tommy Stanek, leader of the GMS finalist team in the ongoing Wisconsin Innovation Awards. "When companies invest in more materials than they need and don't choose sustainable disposal methods, they will either waste their own money or end up overcharging their clients, ultimately damaging the relationship and potentially missing out on future customers that could have been acquired through word-of-mouth recommendations."
Reputation loss is just the start of trouble for teams in this industry. When companies overestimate how many materials they need, they are also more likely to overestimate how many labor hours the project will require. Companies bring on enough team members to manage the resources and navigate on-site situations, but roughly one-third of them will spend their time on non-optimal tasks, like managing conflicts, seeking out higher volumes of materials than necessary, or even moving materials that will ultimately not be used. The scheduling-driven GMS system provides support for managing all resources, including both materials and staff.
"After the project is done, the losses continue. Construction teams will end up with a number of materials that will then need to be transported to a new location and then disposed of, once again driving the cost of the process higher than necessary," says GMS co-founder Stanek. "The less waste a construction company has, the less likely it is to continue spending after a project is finished."
Although the construction industry is known for producing a high volume of waste, it is important to remember that it also has a lot of power to reduce total global waste when it comes to transportation, raw materials, and natural resources. Companies in this industry that go green can have a large and measurable impact, which is an effective way to improve public standing. More consumers are choosing businesses that prioritize sustainable practices, and making these changes can be as easy as choosing a system that prioritizes resource management.
At the center of the Graceful Management System is predictive modeling, which uses the power of artificial intelligence to calculate how much a project will cost, what it will require, and how long it will take. With its ability to analyze several key points from a subscriber's data, it can provide step-by-step instructions to help companies reduce waste, manage costs, and speed up a project timeline. Offering an adaptive solution that can recalculate autonomously as needed to address unexpected circumstances, GMS empowers construction teams to optimize their planning and adapt in record time.
Artificial intelligence is reworking projects in many of the modern world's top niches, and the powerhouse of the construction industry has plenty to gain from these systems as well. Graceful Management Systems can help companies increase their estimation accuracy by up to 95%, reduce overall labor costs by up to 30%, and eliminate up to 25% of construction material waste. Using real-time data and analysis, GMS keeps a pulse on the project and helps companies adapt as needed, making it easy for them to communicate changes with concise solutions to their customers.
There is no doubt about it—when construction teams go green, everyone wins.
ⓒ 2025 TECHTIMES.com All rights reserved. Do not reproduce without permission.