Wooden lights and guitars have been 3D printed by HagenHinderdael, a London-based company that works at the interface of sustainable design, architecture, and cutting-edge technology.
However, it is worth noting that the raw material for these products is rather unusual. It belongs to the low-quality range of lumber and continues to be one of the major environmental ills in existence - sawdust.
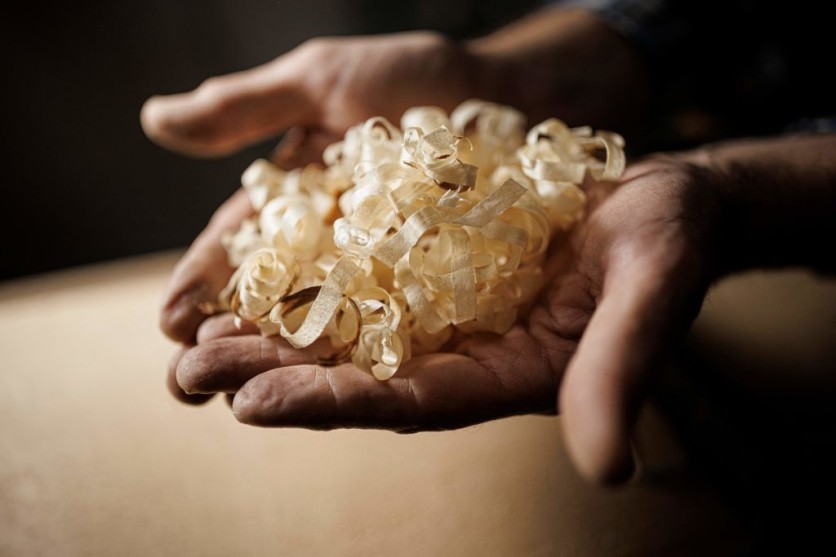
Sawdust and a Binder-Jet Printer
ZDNet reports that HagenHinderdael delivered its lamp rendering to Forust, which was later bought by 3D printing king Desktop Metal in 2019. Forust subsequently printed the lamp using sawdust and a binder-jet printer.
Forust started from a collaboration of three people: namely Andrew Jeffrey, former president of Boston Ceramics, Ronald Rael from the Department of Architecture at the University of California Berkeley, and Virginia San Fratello from the Department of Design at San Jose State University.
They were all part of the San Francisco-based 3D collective Emerging Objects. The collective has experimented with unlikely materials, such as salt and repurposed tires, to create spectacular works of utilitarian art.
The group then concentrated on wooden printing items, a 3D printing problem that has remained unsolved to this point. Their main motivation was to incorporate that strategy into a sustainable solution.
Read also : Engineers Develop a Novel Nanoscale 3D Material That Can be Produced at a Speed of 100 mm/s
3D Printing Solution for Sawdust
Forust's industrial 3D printing solution aims to reduce at least the 84 million tons of sawdust produced by the furniture sector that is either burned or thrown in landfills.
Water-based ink is injected by the printhead that can imitate almost any type of wood grain, including mahogany, rosewood, zebrano, and ebony.
Layer by layer, the ink and binder are injected and deposited by the 3D software-determined rendering contours.
The print head can increase its height by up to 4.5 of an inch every hour until it reaches the completed level.
The leftover sawdust in the box is then gathered for the following project, and a non-toxic, bio-epoxy resin is infused throughout the entire piece to strengthen it.
According to ZDNet's report, these 3D-printed wood components are similar to real wood since they can be polished, coated, sanded, and many more.
The success of Desktop Metal heavily relies on how simple it will be for several businesses to switch from polymers and plastics to environmentally friendly wood components.
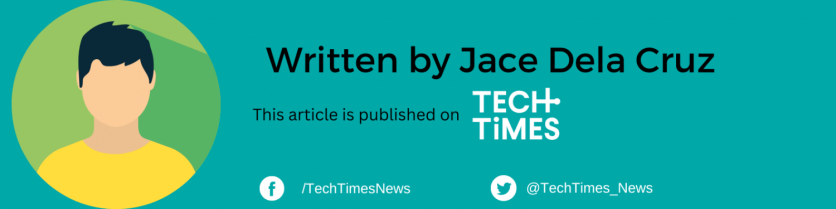
ⓒ 2025 TECHTIMES.com All rights reserved. Do not reproduce without permission.