Rapid 3D printing technologies that can swiftly produce new objects out of a variety of materials may still seem like science fiction. This is because there is still a limited selection of material quality and types available for 3D printing, especially when printing at very tiny scales.
Researchers at Stanford have created a novel material that allows for printing at the nanoscale, producing structures that are only a small portion of the width of a human hair. They have utilized this material to print tiny, lightweight lattices.
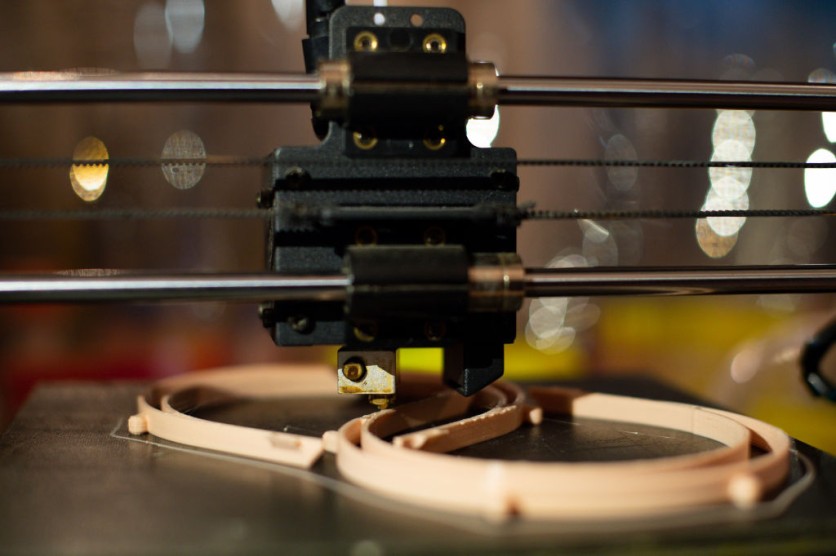
Faster 3D-Printing
The researchers showed in a report that was published in Science that the novel material can absorb twice as much energy as conventional 3D-printed materials of a similar density. Future satellites, drones, and microelectronics could benefit from improved lightweight protection made possible by this new invention.
The team added metal nanoclusters-tiny groupings of atoms to its printing medium to create a superior material for 3D printing.
The printing process used by the researchers, known as two-photon lithography, hardens the printing medium through a chemical reaction sparked by laser light.
They discovered that their nanoclusters were particularly effective in kicking off this reaction, which produced a substance that was a mixture of the metal and the polymer printing medium.
The team was able to mix proteins, acrylates, and epoxies-a few common kinds of polymers used in 3D printing with metal nanoclusters.
The printing process was accelerated by the nanoclusters as well. For instance, the engineers were able to print at a speed of 100 millimeters per second using nanoclusters and proteins, which is roughly 100 times quicker than what had previously been possible with nanoscale protein printing.
A mix of Energy Absorption, Strength, Recoverability
All the constructions with the nanocluster-polymer composite showed a remarkable mix of energy absorption, strength, and recoverability, according to the researchers.
"The lattice structure certainly matters, but what we're showing here is that if the material it's made out of is optimized, that's more important for performance," Wendy Gu, co-author of the paper, said in a press release statement.
"You don't have to worry about exactly what the 3D structure is if you have the right materials to print with."
Gu and her coworkers are in some ways imitating what nature has already mastered. For instance, the mix of a hard exterior, nanoscale porosity, and small traces of soft substance gives bone its durability.
Our bones can transport energy most of the time without breaking and remain reasonably lightweight thanks to their 3D structure and variety of well-designed materials.
To better spread an impact and prevent crushing, 3D-printed protective constructions should also contain several types of material, some tougher and some softer.
Related Article : 3D Printed Skull for a Newborn Saved Her Life-Complex Process Answered by Engineers and Doctors
This article is owned by Tech Times
Written by Jace Dela Cruz