Nanoracks revealed more details and demonstrated cutting metal in orbit, as reported by TechCrunch. The experiment was conducted back in May and its parent company Voyager Space, after getting to orbit aboard the SpaceX Transporter 5 launch. It was only on Friday that the company released additional details.
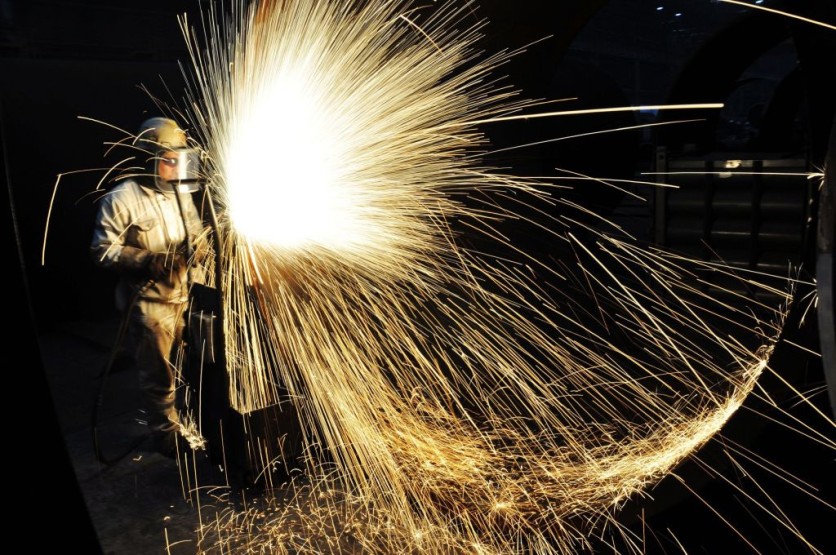
The goal of Outpost Mars Demo-1 mission was to cut a piece of metal that is like the outer shell of United Launch Alliance's Vulcan Centaur and common in space debris, via friction milling. The demo lasted around a minute and it was successfully completed.
The demo was in partnership with Maxar Technologies. Maxar Technologies is the one who developed the robotic arm that executed the cut, through a commercially available friction milling end effector. The whole structure was contained in the Outpost spacecraft to ensure that no debris escaped.
Welding on Earth is messy, but thanks to gravity, the dust and debris just fall to the ground. In space, it's a whole different thing. The debris should be contained to keep your work area clean. In fact, one of the goals of the demo was to produce no debris.
Apparently, the idea of cutting metal in space has been around for quite a while. However, this is the first time that the idea has been turned into a reality. Cutting metal in orbit is a tricky task and it's not something that can be done by any old robot arm. Oxygen and other flammable materials will be available in small quantities, so any sparks would have to be kept to an absolute minimum.
In space, you don't have gravity like you do on Earth. This means that you can't use your trusty welder to do the job. The friction reduction will happen because the metal is incredibly hot.
The friction will be enough to cut through the metal, but you need to keep the temperature controlled. In fact, keeping the temperature high enough is a problem in itself. A typical red-hot welder would increase the temperature at a rate of around 100 degrees per minute.
In space, a welder can't maintain the temperature for much longer than a few minutes before the metal cools down. In order to cope with this issue, the friction milling machine uses electrical heating elements to keep the temperature.
Future Plans
Aside from the Outpost program, Nanoracks and Voyager partnered with Lockheed Martin to develop a commercial space station that will be called Starlab. They were chosen by NASA to further enhance its plans under the agency's Commercial low Earth orbit Destinations program.
These opportunities could revolve around space tourism, microgravity manufacturing, research, and even space solar power. In the future, Starlab will be expanded and added more modules to allow more astronauts to be accommodated.
Related Article: US Says ISS Deadline Could Affect Humans in Orbit-Authorization Bill Required for NASA? Other Space Issues Being Discussed
This article is owned by Tech Times
Written by April Fowell
ⓒ 2025 TECHTIMES.com All rights reserved. Do not reproduce without permission.