
The world is changing rapidly with the development of information technologies. Mechanical engineering is no exception. Digital technologies are being introduced into all areas of production, transforming it from the ground up, which leads to increased efficiency, improved product quality, and new opportunities for innovation. But behind this revolution lie a number of questions: How will IT change the engineering job market? What skills are going to be needed? Seeking answers to these questions is Andrey Aksenov, one of the leading experts on the digitalisation of mechanical engineering.
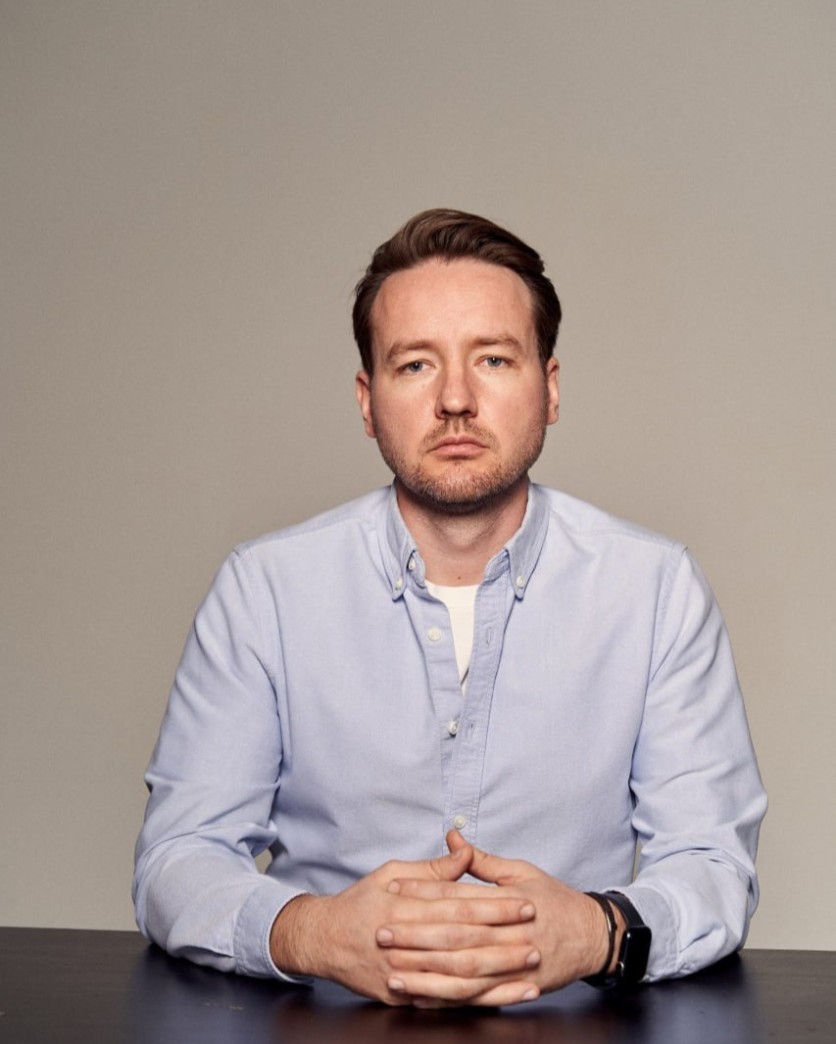
In this interview, he shares his experience, talks about projects he has implemented, and offers his vision for the future of the industry.
Andrey, thanks for meeting us to discuss how IT is transforming mechanical engineering. You have a reputation as one of the world's foremost experts in the field, and rightly so. Can you tell us how you got into the field and what fascinates you about it?
— I started my career in the IT field when I was still a student at university. I was involved in process automation at a mechanical engineering company. It was then that I realised that technology could not only make work more efficient but could also create completely new opportunities. And I found myself drawn to it. The first task I was given was quite simple—to automate the creation of the process documentation. But as time went on, the tasks became more and more complex and interesting. I became interested in learning new technologies and immersed myself in the world of programming and data analysis. Later, I became the head of the Automation Department and began to manage developing and implementing IT solutions for the whole company. It was then that I realised that IT was not just a tool but a powerful force that could change the world of production.
The originality and efficiency of your projects are well known. What have you been able to implement in the field of digitalisation in mechanical engineering that has produced tangible results?
— Implementing solutions that help companies become more competitive and efficient is one of my main tasks. We've implemented a number of projects related to automating manufacturing processes, enterprise management systems, big data analytics, and artificial intelligence. And every one of them has had a positive impact.
Come and share. What specific solutions have been introduced?
— The implementation of a predictive maintenance system is a prominent example. To predict equipment failures long before they occur, we use machine learning to analyse sensor data. This allows us to schedule maintenance well in advance, minimising downtime and reducing repair costs. In the early years, we even designed and implemented a neural network to automate production preparation before the technology even existed. To help us make better data-driven decisions, we also undertook major projects to implement business intelligence (BI) systems. This included developing and implementing BI dashboards, improving data collection and processing systems, and securing data. The development of fleet management systems using telematics data was also a significant investment. As a result, we were able to optimise routes, reduce fuel consumption and improve driver safety.
In your opinion, what will be the most promising areas in the field of machine automation?
— I see great promise in developing artificial intelligence and machine learning. These technologies will be instrumental in the creation of smarter production lines, the automation of complex operations, and the improvement of product quality. For example, we are currently working on a project that will use artificial intelligence to automate the process of quality control. The system will analyse camera images and identify defects at an early stage of production, preventing waste and reducing the cost of correcting errors. The Internet of Things (IoT) will also continue to develop, enabling a fully integrated manufacturing system in which all devices and processes are connected to each other and share data.
But the question inevitably arises as to the impact of automation on the labour market. Is it going to lead to downsizing?
— I am sure that automation will not lead to mass redundancies. Rather, it will redistribute the workforce. Many routine tasks will be automated, but this will free up workers for more creative and intellectual tasks related to design, innovation, and management. For example, instead of routinely monitoring a machine, an operator will be able to focus on analysing data, optimising the production process, and developing new technological solutions. Sure thing, this means retraining people, but it is an inevitable process that will help the engineering industry to remain competitive in the modern world.
As IT evolves, what skills will be in demand in the engineering industry of the future?
— Professionals of the future will need an understanding of manufacturing processes and the ability to work with modern equipment, as well as a wide range of skills, including programming, data analysis, and machine learning. Also, complex problem-solving, adapting rapidly changing technologies, and teamwork are essential. Predictive maintenance implementers, for example, will need to have a good understanding of equipment in order to correctly interpret sensor data and understand what actions need to be taken to prevent breakdowns, as well as being skilled in machine learning and data analytics.
And what about cybersecurity issues? New threats emerge with the introduction of IT in production. How do you address this problem?
— Cybersecurity is a critical issue for any business, and the engineering industry is no exception. We constantly update our security systems and closely monitor the emergence of new threats, investing a lot of resources in developing this area, training specialists, and implementing advanced solutions to counter cyber-attacks. In addition, we're developing security systems that are integrated with other production systems, allowing us to respond to potential threats in a timely manner and prevent access to data.
What other important IT trends in the engineering industry could you point out?
— Another important direction is the development of digital twins. These are virtual models of real objects that you can use for the simulation of production processes and virtual testing of new solutions. That means less time and money spent developing and implementing new technology. For instance, this allows us to create a digital twin of a new machine, testing the machine in a virtual environment before going into production and also allows us to identify potential problems and improve the design of the machine before it is physically manufactured.
Andrey, many thanks for this interesting interview. What would be your final words of caution?
— The digital revolution in mechanical engineering has already begun. IT is becoming the key to success in this industry. Embracing new technologies will allow us to create better products, improve productivity, and remain competitive in the global market. In the years to come, there are bound to be other bright and innovative projects in IT and machine building; I am sure of that.
ⓒ 2025 TECHTIMES.com All rights reserved. Do not reproduce without permission.