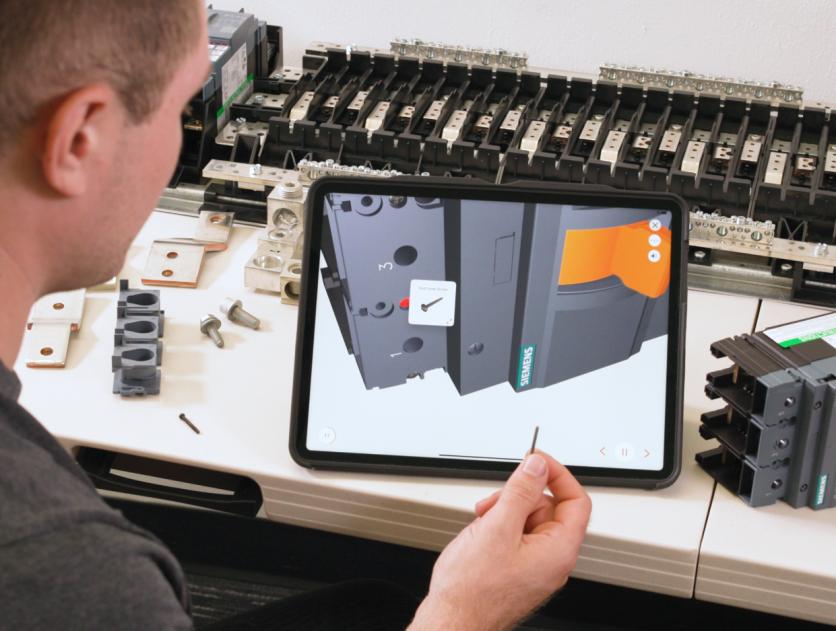
The technology and science of interactive 3D training has come to manufacturing. And its arrival isn't a minute too soon.
The sector has changed, partly due to the so-called "graying" of America. As older employees retire, they leave sizable knowledge gaps behind. It is projected the manufacturing industry will face a labor shortage of 2.1 million workers by 2030. However, an aging workforce isn't the only issue making manufacturing tumultuous. Another problem is high turnover.
Within manufacturing, the annual employee churn hovers around 28%. While it's less daunting than rates for other industries like hospitality and construction, it's a costly reality when more than one-quarter of your workforce leaves every year.
This is where flexible, tech-forward 3D work instructions come into the picture. With immersive technology, manufacturers are revitalizing employee training programs to simplify onboarding and standardize induction protocols. That way, they can retain the people they hire and educate a new generation of manufacturing leaders and innovators.
The Impact of Training on Manufacturing Efficiency
Why put such an emphasis on training to solve manufacturing's labor dilemma? Research shows extended reality (XR) training is a solid way to attract and retain workers.
In a recent survey of training managers, 81% agreed that XR modules increase employee confidence and cultivate muscle memory. Of those surveyed, 67% said XR training allows employees to complete onboarding faster, which catalyzes productivity. When employees take more responsibility for their work quality, performance, and productivity, they're less likely to make preventable errors.
Ultimately, the type of training that will play a pivotal role in the manufacturing industry isn't the methods of the past, and stakeholders agree. A recent study by Wakefield Research found that 89% of executives worried that their technical training wasn't working well.
Here's the truth: Modern workers respond to tech-forward training over static paper instructions and old-school lecture sessions. Traditional book learning and long-form video modules don't appeal to most workers anymore. That's why BILT developed an interactive 3D work instruction platform.
A Leading-Edge Technical Training Solution
To understand how revolutionary BILT's tech-driven digital work instruction software is, consider the historical approach. Since the Industrial Revolution, manufacturing job training has evolved from informal apprenticeships to formalized programs. Initially, workers learned on the job, but as factories expanded, standardized training emerged.
Mid-20th-century training adopted military techniques, combining classroom instruction with practical experience. The late 20th century's automation boom necessitated specialized technical training. In the 21st century, digital tools like e-learning, virtual reality, and augmented reality have galvanized training, providing immersive and interactive experiences.
BILT guides users with cutting-edge technology: interactivity and spatial computing. The work instruction software as a service has two solutions: 3D interactive instructions for smartphones and tablets, and immersive instructions for the Apple Vision Pro. No delays, no downtime—just a straightforward way to learn that enables easier set-up, maintenance, and repair.
Manufacturers can leverage the expertise of BILT's digital work instructions to educate employees with voice, text, and animated image guidance. Bite-sized steps guide each project with warnings, tips, tools, and parts clearly defined so users can immediately become successful on new tasks.
Best of all, once downloaded, the guide lives in perpetuity on the user's mobile device or headset, making it accessible 24/7 from anywhere without Wi-Fi. Updates to instructions can be downloaded in real-time the next time a user has connectivity, so the digital guides are never obsolete.
By leveraging innovative training, manufacturers can pass along key information and directions to their employees at scale. This enables predictable—and budget-friendly—resource allocation. At the same time, BILT guides can be constructed to align worker training with the overall corporate vision of the manufacturing company.
Benefits of 3D Work Instruction Software
If you're intrigued by this next-level training, you're not alone. Hundreds of brands trust BILT to produce high-quality, sustainable work instructions. In addition to giving employees more engaging training, there are other tangential benefits.
1. Attract Young, Tech-Savvy Workers
Manufacturing has become an increasingly technical field. Younger workers are digital natives. According to a survey by Adobe, experts say 70% of Gen Z employees would leave their current jobs for better technology.
Companies that onboard with 3D work instructions meet these trainees where they are most comfortable and competent: on their mobile devices. By delivering interactive, customizable guides to their phones, workers can have easy access at their fingertips.
2. Train Individuals at Their Own Pace
When workers have the freedom to learn when it's best for them, they are less distracted and more focused on the content they're reviewing. They don't have to be afraid to ask questions or request a review of the material, either.
Trainees can continue reviewing tasks as long as they need to feel competent in a skill. They can alter the 3D animations to view from any angle in case they're looking at equipment from a different perspective.
3. Capture Training Data and Identify Trends
Implementing work instruction software makes it possible to harness vast pools of data. BILT gathers analytics on user performance. Insight into these metrics allows trainers and program managers to work with instruction designers to update training continuously.
Manufacturers that use digital work instruction software can access this data to evaluate performance and competency. Trainees can also provide feedback on products and procedures to help instruction designers enhance clarity and comprehension.
Though manufacturing companies are going through some challenges, they aren't without options. By updating their training to include digital work instruction software, they can reduce turnover, attract talented job seekers, and keep moving toward a more productive future.
ⓒ 2025 TECHTIMES.com All rights reserved. Do not reproduce without permission.