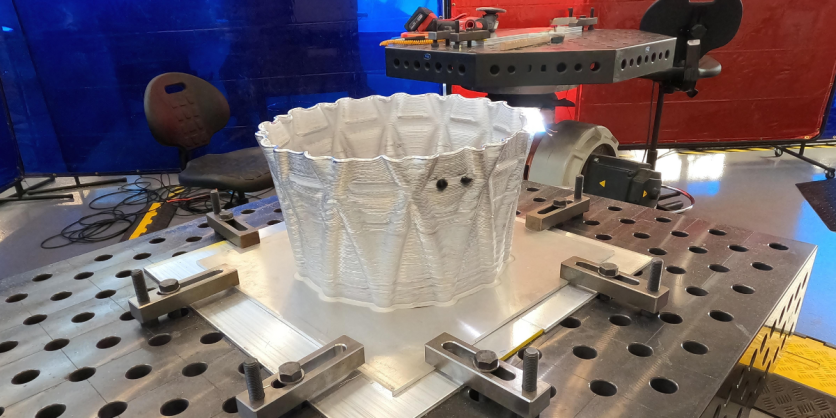
Additive manufacturing, or 3D printing, has emerged as a significant innovation in aerospace manufacturing. It enables the creation of intricate parts with remarkable precision and ease. Beyond simply expediting production, 3D printing is reshaping design practices, material selection, and supply chain management in aerospace manufacturing.
Solideon is at the forefront of aerospace manufacturing innovation with its latest technology, Aperture. Aperture marks a significant advancement in aerospace manufacturing, allowing for swift production of intricate structures with fewer parts, less waste, and greater precision. This collaborative robotic system combines additive manufacturing with CNC machining and advanced inspection features, offering a complete solution for crafting top-notch aerospace components.
Traditional manufacturing lead times present several challenges for aerospace companies, including lengthy production schedules, high costs, and limited design flexibility. These challenges stem from the reliance on conventional manufacturing processes, such as casting and machining, which require specialized tooling and extensive setup times. Additionally, outsourcing parts to multiple suppliers can further extend lead times and increase the risk of delays.
Unlike traditional manufacturing methods, which rely on subtractive processes like cutting and drilling, Aperture builds components layer by layer, eliminating the need for complex tooling and reducing setup times. Integrating multi-robotic capabilities into a collaborative manufacturing cell allows Aperture to achieve high levels of automation and efficiency, allowing for faster production of complex aerospace components.
"Traditionally, manufacturing is segmented. People are focused on printing components, which are then taken to somebody else to integrate. We have a multi-robotic system in Aperture because we want to combine as many manufacturing processes, post-3D printing, into our cell as possible." says CEO Oluseun Taiwo.
The motivation behind printing one of the world's largest 3D steel structures stemmed from Solideon's goal to demonstrate the capabilities of its Aperture technology. With long lead times and manufacturing constraints, Solideon decided to print its components to expedite the process and showcase its technical readiness. The project served as a testbed for Solideon's advanced algorithms, 3D printing capabilities, and material properties, highlighting its ability to handle complex manufacturing challenges and deliver high-quality products quickly.
Utilizing advanced algorithms for design optimization, Solideon employs machine learning and generative design techniques to enhance component performance and efficiency while reducing costs. This approach allows for the creation of lightweight yet robust components tailored to meet specific requirements. This AI platform allows Solideon to automate a large portion of the design engineering process and rapidly deploy hardware at the speed of software.
Additionally, Solideon, alongside its partners at Texas A&M University, has spearheaded the creation of exclusive techniques for 3D printing gradient materials, facilitating smooth transitions between various metals within one component. This advancement leads to parts with unparalleled mechanical qualities, boosting durability and reliability in aerospace uses.
Solideon leverages real-time feedback loops and digital twin technology to ensure the quality and accuracy of its manufacturing processes. By capturing and analyzing data in real-time, Solideon can make immediate adjustments to optimize printing and assembly, reducing errors and improving overall product quality. Solideon's use of off-the-shelf robotics, and proprietary software means aperture is scalable, and is forwardly deployable in the long term.
Solideon's vision for the future extends beyond terrestrial applications to include manufacturing in space. The company aims to develop further autonomous manufacturing systems capable of constructing entire products in space, ultimately facilitating the establishment of sustainable human presence beyond Earth. This vision aligns with concepts such as space colonization and resource utilization, where in-space manufacturing could enable the production of infrastructure, habitats, and spacecraft components using local resources.
"The goal for Solideon is to get to space and be the first company to manufacture entire products in space, for space," states Taiwo.
Solideon's approach to manufacturing presents possibilities for future collaborations with other aerospace companies, research institutions, and government agencies. By partnering with stakeholders across the industry, Solideon can leverage collective expertise and resources to advance its technology further and explore new applications in space exploration and beyond.
Overall, Solideon's vision for the future of manufacturing on Earth and in space has far-reaching implications for industries worldwide. By pushing the boundaries of what's possible with Aperture technology, Solideon is poised to shape the future of aerospace manufacturing and contribute to humanity's exploration and utilization of space. To learn more, visit solideon.com.
ⓒ 2025 TECHTIMES.com All rights reserved. Do not reproduce without permission.