The U.S. Department of Energy's National Renewable Energy Laboratory (NREL) has employed robotic technology to assist in the production of wind turbine blades, aiming to alleviate challenging working conditions and enhance product uniformity.
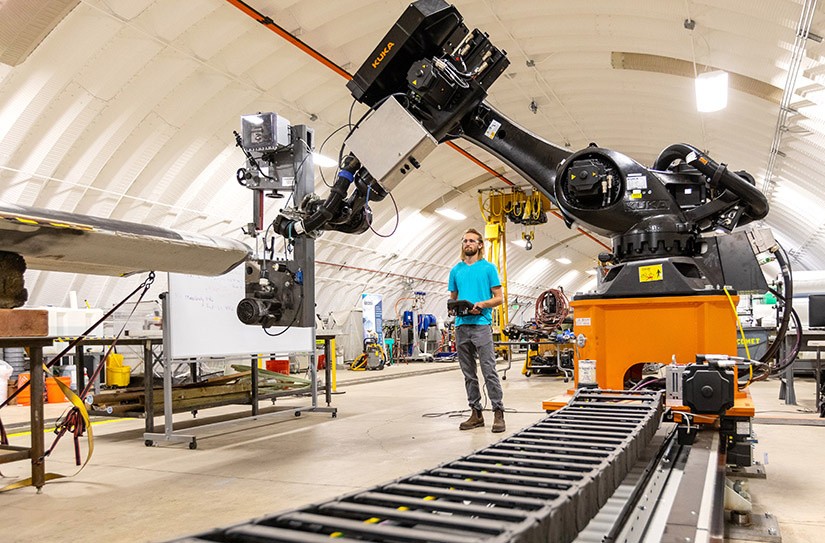
Robots Offer Helping Hand in Creating Wind Turbine Blades
Robots have been utilized in the wind energy sector for tasks like painting and polishing blades, but automation has not seen widespread adoption.
Recent research at NREL demonstrates a robot's capability to perform essential tasks like trimming, grinding, and sanding wind turbine blades after the fabrication process, which involves molding and bonding the blade sides together.
Hunter Huth, an NREL robotics engineer and the study's lead author, described the project as successful despite the operational challenges encountered.
The researchers note that wind turbine blade manufacturing involves labor-intensive post-molding operations that often require workers to perch on scaffolding and wear protective gear. Automating these tasks is expected to enhance worker safety and retention by streamlining operations.
Daniel Laird, director of the National Wind Technology Center at NREL, emphasized the significance of this work for U.S.-based blade manufacturing.
According to Laird, automating labor-intensive tasks could enhance the economic viability of domestic blade production compared to imported blades, which are often manufactured offshore due to high labor costs.
Huth emphasized the research's aim to develop automation methods that render domestically manufactured blades more competitive on a global scale.
The researcher explained that offshore blade manufacturing in the U.S. faces challenges due to labor-intensive processes and high worker turnover rates, making automation more necessary than ever.
The research took place at NREL's Composites Manufacturing Education and Technology (CoMET) facility at the Flatirons Campus.
While a robot was deployed to work on a 5-meter-long blade segment, programming for larger blades would require a section-by-section approach due to their structural characteristics.
To ensure precision, the researchers used scans to create a 3D representation of the blade's position, determining key sections of the airfoil.
Subsequently, the robot was programmed to execute specific tasks and evaluated based on accuracy and efficiency.
Read Also : Transform Outdoor Adventures: Dnsys X1 Exoskeleton Makes Hiking, Climbing, and Running Easier Than Ever
Automation in the Wind Energy Sector
Areas for improvement were also identified during the research, particularly regarding the grinding process, where the robot exhibited inconsistencies in material removal across different sections of the blade.
Huth emphasized that automation offers consistency in manufacturing, a challenge when relying solely on human labor. Additionally, robots can utilize more abrasive materials, optimizing efficiency beyond human capability.
"This work is critical to enable significant U.S.-based blade manufacturing for the domestic wind turbine market," Laird said in an official statement.
"Though it may not be obvious, automating some of the labor in blade manufacture can lead to more U.S. jobs because it improves the economics of domestic blades versus imported blades."
The findings of the research team were published in the journal Wind Energy.
Related Article : This Remotely-Controlled Robot Can Revolutionize Underwater Missions With 'Fin-Tastic' Features
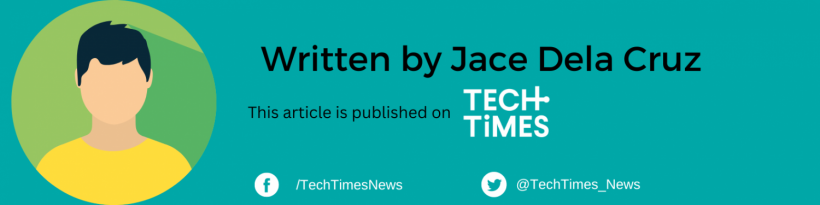