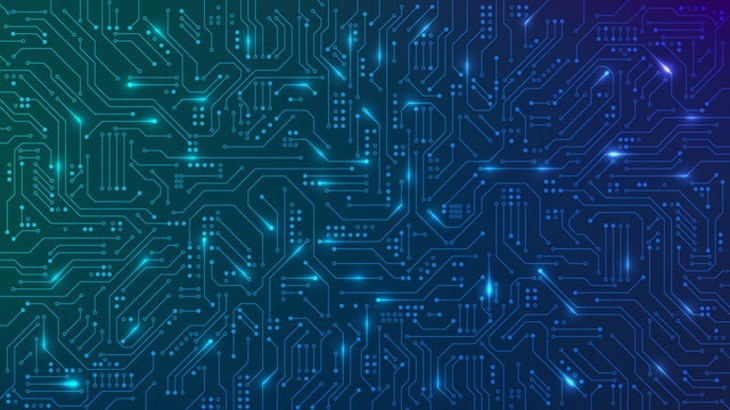
Founded by engineers Robert Lane and Alan Liao, Manaflex was born out of a shared dissatisfaction with the status quo of circuit manufacturing processes, notably chemical etching and stamping. Chemical etching is often criticized for environmental waste and unhealthy working conditions for employees.
The co-founders envisioned a company that could disrupt traditional circuit technologies through advanced manufacturing methods, such as substituting precise lasers for environmentally harmful chemicals and switching from copper to aluminum. This vision has since been translated into concrete achievements, with Manaflex developing solutions not only for leading multibillion-dollar technology corporations but also for smaller firms across various sectors, including electric vehicles, energy, VTOL, aerospace, and consumer electronics. Its growing intellectual property portfolio now includes over 20 patents and pending patents.
Environmental Benefits of Laser-Based Manufacturing
Manaflex's shift toward laser technologies for manufacturing circuits represents a significant step forward in reducing the environmental impact of circuit production. Traditional methods such as chemical etching and stamping have been the industry standard for years but come with considerable environmental and health drawbacks.
Chemical etching involves applying a protective layer to parts of a metal surface and then bathing the metal in a chemical solution that eats away at the unprotected areas. It requires substantial quantities of chemicals, some of which are hazardous.
Unlike chemical etching, utilizing lasers doesn't rely on hazardous chemicals to create patterns on the substrate. Lasers precisely ablate material to form circuits without the need for chemical baths, significantly reducing the generation of hazardous waste.
"There's a human cost and a world cost to these chemicals, and they are generally less efficient in terms of energy use," says Lane. "When you use all these chemicals, you have to produce them too. There's significant energy also associated with that chemical production. Then you have to recycle them afterward with a potentially hazardous type of recycling method."
Lane continues, "Lasers are energy, but the benefit of lasers is that they can be controlled very well. So you have control, and you can be more efficient with a laser. That's the whole idea."
Lasers can be highly energy-efficient, operating at lower temperatures than those needed for traditional manufacturing processes and targeting very specific areas with minimal waste to optimize energy use.
Both chemical etching and stamping can lead to material wastage. Chemical etching removes material across the entire bathed area, not just where the circuit paths are needed. Stamping, while precise, can lead to excess material from the punched-out areas that may not be easily recyclable. Stamping also requires more human labor as part of the manufacturing process. The precision of lasers means that material is only removed or altered where necessary, minimizing waste. This precision also allows for the production of more intricate and densely packed circuits, improving the efficiency of material use.
Finally, chemical etching exposes workers to potentially harmful substances, necessitating strict safety protocols and protective equipment to mitigate health risks. Manaflex favors an approach that emphasizes lasers and integrates automation. This reduces workers' exposure to hazardous chemicals and ultimately results in a safer work environment.
Transitioning to the Sustainability of Aluminum
"One issue is that the materials that we use to produce circuits have to be able to be broken down and recycled. Anything that we have that is wasteful, that needs to be recycled, anything that goes into a product, you need to think about how you would be able to break it down later and recycle it," says Lane, explaining Manaflex's choice to use aluminum. "And I think that the interesting thing about circuit production is that we have full visibility into it. We can focus on our principles, and we can select materials, such as aluminum, that can meet the technology requirements of our customers, but also select materials that are recyclable."
Aluminum recycling requires just 5% of the energy used to produce the primary metal, which further enhances its sustainability profile. By transitioning to aluminum, manufacturers can decrease the environmental impact of their products without sacrificing performance.
Demand for aluminum is expected to surge by nearly 100 net pounds per vehicle from 2020 to 2030, driven primarily by the shift toward electric vehicles that rely on aluminum to maintain fuel efficiency without sacrificing performance or safety. EVs' share of production nearly doubled from just under 3% in 2020 to approximately 6% in 2022, with expectations to exceed 36% by 2030.
Automation and Sustainability in Manufacturing
For Manaflex, the integration of automation into its advanced manufacturing processes presents another avenue for reducing environmental impact. Automated production lines can achieve higher precision and efficiency than manual processes, leading to lower rates of material waste and energy consumption. Automation also enables more consistent quality control, reducing the need for rework and further decreasing the amount of waste generated.
Additionally, automation allows for the optimization of manufacturing processes in real-time, adjusting for variations in material properties or environmental conditions. This adaptability ensures that resources are used as efficiently as possible, minimizing excess energy consumption and material usage. As a result, the environmental footprint of circuit manufacturing can be significantly reduced.
FPCs and Efficient Energy Storage
Manaflex's product offerings, specifically aluminum-based flexible printed circuits for clean energy storage, position the company as a significant contributor to the clean energy sector. These FPCs are crucial for various applications, including EVs and renewable energy storage solutions, where efficiency and sustainability are paramount.
By manufacturing these components with these environmentally friendly strategies, Manaflex is working to both advance the technological capabilities of clean energy storage solutions and promote a new production process that aligns with broader sustainability goals. From medical devices to consumer product industries, the global growth of new electronics will demand more collaboration for more sustainable approaches to circuitry manufacturing from new startups, established corporations, and other players in the technology ecosystem.
ⓒ 2025 TECHTIMES.com All rights reserved. Do not reproduce without permission.