Aurora Flight Sciences, a subsidiary of Boeing, is moving through Phase 1B of the Liberty Lifter program, a project initiated by the Defense Advanced Research Projects Agency (DARPA) to create an affordable seaplane with revolutionary heavy-air-lift capability from the sea.
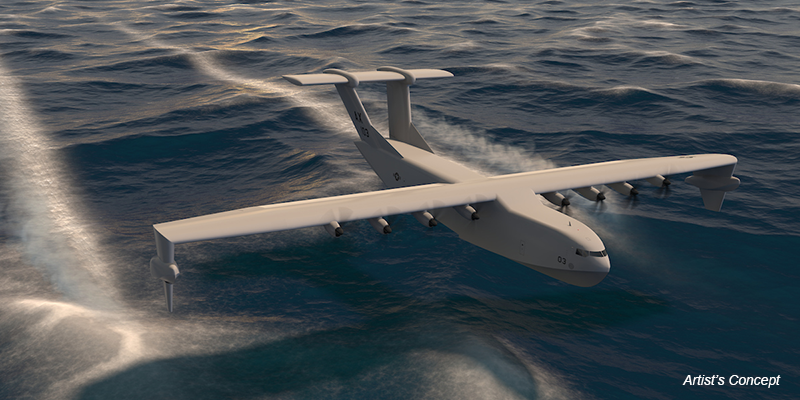
All About the Liberty Lifter
The Liberty Lifter aims to combine the cargo volume of a C-17 Globemaster III transport aircraft with the capacity to carry 100 tons of cargo over a ferry range of 6,500 nm (7,500 miles, 12,000 km).
"Innovations often occur at intersections. Here, it's the intersection of our maritime and aerospace teams," said Dan Campbell, Aurora program manager.
"For example, the intersection of maritime manufacturing with aerospace structural design, or the intersection of maritime wave forecasting with aerospace controls," Campbell added.
The ongoing development focuses on risk reduction during the preliminary design phase, with an emphasis on low-cost manufacturing methods.
Aurora's Collaboration With ReconCraft
Aurora Flight Sciences collaborates with ReconCraft, an Oregon-based shipyard, to build full-scale structural test articles, including a section of the fuselage.
This approach aims to minimize risk and ensure quality as the team explores novel materials and unique design requirements. A significant aspect of Phase 1B involves testing for risk reduction, with ReconCraft contributing maritime manufacturing expertise.
The team has shifted the design from a t-tail to a pi-tail for improved structural efficiency, especially with regard to accommodating an aft cargo door.
Additionally, the relocation of floats from the side-sponsons to the vehicle's wing tips enhances the balance between vehicle affordability and performance in the ground effect.
Read Also : DARPA Partners With Raytheon to Develop Revolutionary Air-Breathing Rotating Detonation Engine 'Gambit'
Liberty Lifter's Capabilities
The Liberty Lifter's capabilities involve operating efficiently in ground effect at high sea states, and it employs low-cost manufacturing and unique design features to achieve affordability.
Testing includes evaluating slamming during landing using a scale model of the hull in the tow tank at Virginia Tech. Future testing will incorporate flying sensors and software for wave detection and prediction, contributing to the advanced control system for safe flight in ground effect over high sea states.
The collaborative effort includes ReconCraft, Gibbs & Cox (a Leidos company specializing in naval architecture and marine engineering), and advisors and engineers from Boeing. The program builds on Boeing's extensive history in seaplanes and flying boats.
Dan Campbell, Aurora program manager, highlights the synergy between maritime and aerospace teams, emphasizing the innovative intersections of maritime manufacturing with aerospace structural design and maritime wave forecasting with aerospace controls.
The expected completion of Phase 1B involves a preliminary design review tentatively set for January 2025. If the program advances as planned, the subsequent phase may involve flight testing in 2028, according to Aurora Flight Sciences.
Related Article : Boeing Is Developing Hypersonic Interceptor Prototype Designed to Destroy Incoming Missiles in the Air
