In preparation for future lunar missions, the European Space Agency (ESA) has embarked on a project utilizing high-energy lasers and simulated moon dust to construct viable road surfaces on the lunar landscape.
The lunar environment poses unique challenges, with fine, abrasive, and adhesive lunar dust proving problematic for equipment and spacesuits. According to ESA, historical missions like Apollo 17 had faced overheating issues due to dust accumulation, demonstrating the urgency for practical solutions.
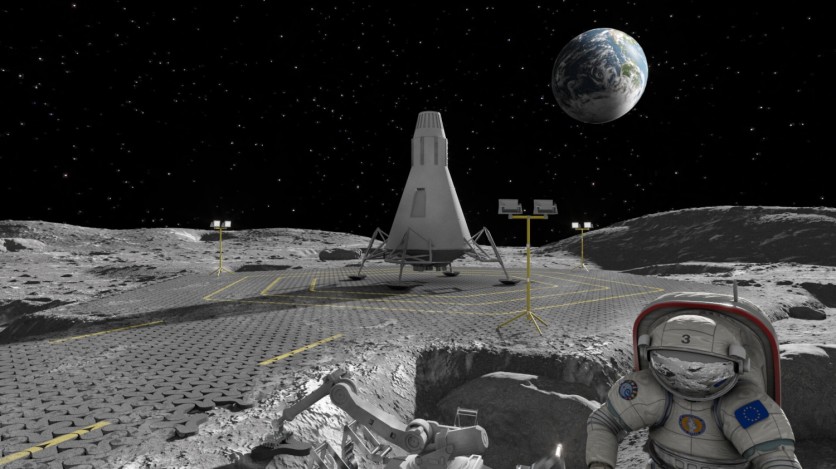
ESA's PAVER
To keep lunar dust at bay, experts proposed paving over high-activity zones, including roads and landing pads. The idea of melting sand to make roads was first proposed for Earth in 1933.
ESA's PAVER (Paving the road for large area sintering of regolith) initiative is at the forefront of lunar roadmaking. Led by Germany's BAM Institute of Materials Research and Testing, in collaboration with Aalen University, LIQUIFER Systems Group, and Clausthal University of Technology, the project explores the feasibility of this approach.
The PAVER team harnessed a potent 12-kilowatt carbon dioxide laser to transform simulated moon dust into a solid, glassy surface, a technique that could revolutionize lunar construction.
Advenit Makaya, an ESA materials engineer, elucidates that while a carbon dioxide laser would not be practical on the moon, the current laser serves as a substitute for lunar sunlight. Concentrating light through a Fresnel lens can achieve equivalent melting on the lunar surface.
Makaya underscores the significance of broadening the focal point for constructing roads and landing pads, emphasizing the need for efficiency and scale in these lunar endeavors. The consortium honed their technique at the Clausthal University of Technology, achieving a spot size of 5 to 10 centimeters.
Through meticulous trial and error, they refined a strategy employing a 4.5-centimeter diameter laser beam, producing triangular, hollow-centered shapes spanning roughly 20 centimeters. These interlocking formations could be assembled into robust surfaces across extensive lunar terrain.
Though glasslike and brittle, the resulting material primarily contends with downward compression forces. Even in the event of breakage, it remains serviceable and can be repaired as needed, according to Makaya.
The team transitioned to designs with minimal crossovers to prevent track cracking upon reheat. Each melt layer measures approximately 1.8 centimeters in depth, with the potential for multiple layers in constructed structures or roads, contingent upon the requisite load-bearing capacity.
Read Also : NASA's Artemis II Moon Rocket Core Stage Nears Completion as It Enters Final Assembly Phase
Large Laser Spots
Jens Günster, who heads BAM's Multimaterial Manufacturing Processes Division, emphasizes the essential role of large laser spots in achieving substantial structural melting.
The team estimates that a 100-square-meter landing pad, with a 2-centimeter-thick layer of dense material, could be completed within 115 days.
This innovative venture originated from ESA's Discovery element, part of the agency's Basic Activities, and was facilitated through the Open Space Innovation Platform (OSIP).
The call, designed to solicit research ideas about off-Earth manufacturing and construction, generated 69 responses. Of these, 23 ideas were implemented and evaluated by an expert panel for novelty.
"This initial call has been an effective investment from our point of view. It has opened up multiple promising tracks for follow-up investigation," said Makaya.
Related Article : Radio Telescope Will Fly to the Moon to Listen for Signals From the 'Dark Ages' of the Universe
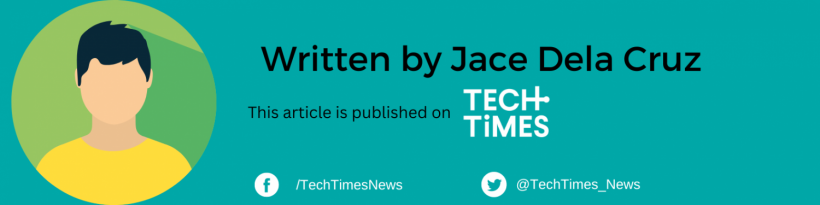
ⓒ 2025 TECHTIMES.com All rights reserved. Do not reproduce without permission.