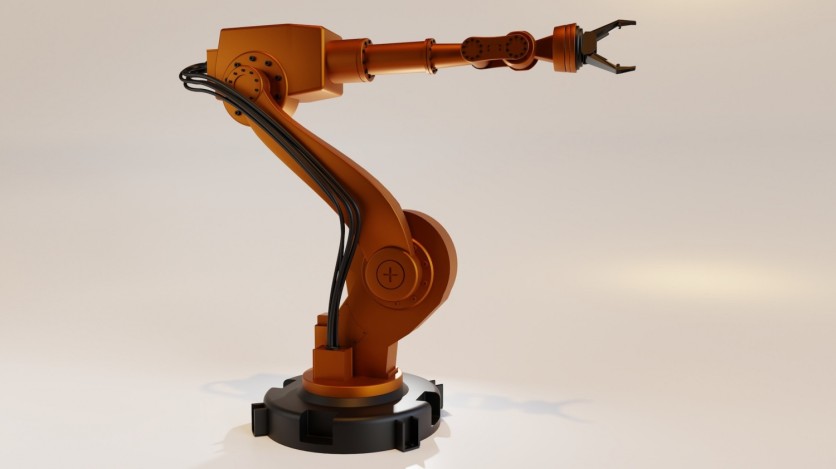
Collaborative robots, better known as cobots, have reshaped the packaging and palletizing industry landscape. These innovative machines are transforming how we handle production, bringing unprecedented efficiency, precision, and safety to the workplace. Unlike their fully automated counterparts, cobots can work alongside human operators, promoting an environment of synergy and cooperation.
In packaging and palletizing, cobots offer many advantages, such as reducing the risk of injury from repetitive tasks, enhancing productivity through round-the-clock operation, and providing flexibility by quickly adapting to various product lines. This article dives into the transformative role of cobots in the packaging and palletizing sector, underlining their importance in the future of manufacturing.
What is a cobot?
Cobots are designed to interact with humans in a shared workspace. This cooperative environment contrasts traditional industrial robots that operate autonomously or with limited guidance and are isolated from human workers.
Cobots execute tasks in tandem with human workers, enhancing the efficiency and quality of output in various industrial processes. They are typically smaller, more flexible, and easier to program than conventional robots. This design makes them suitable for multiple applications, from assembly and packaging to quality inspection and laboratory work.
A key feature of cobots is their inherent safety design. They have sensors and software that enable them to recognize and avoid unintended contact with human workers. They safely stop or slow down if a human comes too close, reducing the risk of accidents.
Cobots are easy to learn, set up, and operate. Most models have user-friendly human-machine interfaces (HMIs) that make programming simple by allowing workers to program and control the robot without extensive technical knowledge. In many cases, a worker can reprogram a cobot simply by putting its arm through the required motions, and the cobot remembers the movements and repeats them independently, without needing a new code.
This ease of use, flexibility, and safety make cobots an increasingly popular choice for businesses looking to optimize their operations and boost productivity.
Cobots represent a significant advancement in robotics and automation. They offer a practical, safe, and user-friendly solution for manufacturers looking to augment their workforce and improve operational efficiency.
What are the advantages of investing in cobots?
Cobots, or collaborative robots, are revolutionizing the packaging and palletizing industry. They come with several distinct advantages:
Increased Productivity: Cobots can operate 24/7 without breaks, significantly increasing output and productivity. They can work faster and more efficiently than humans, reducing the time taken for packaging and palletizing.
Reduced Labor Costs: With cobots taking over repetitive tasks, organizations can save significantly on labor costs. Cobots do not require benefits, leaves, or overtime pay, making them a cost-effective long-term investment.
Improved Safety: Cobots have safety features that prevent accidents and injuries in the work environment. They can take over risky tasks from humans, reducing workplace hazards.
Flexibility: Cobots are easy to program and reprogram, allowing them to perform diverse tasks. This flexibility makes them adaptable to product line or packaging design changes.
Increased Accuracy: Cobots rarely make mistakes, ensuring accuracy and quality in the packaging and palletizing process, reducing the risk of damage and loss, and saving costs in the long run.
Easy Integration: Cobots can be easily integrated into existing production lines, requiring minimal changes to the existing setup. They are compact and need less space than traditional industrial robots.
Employee Empowerment: Instead of replacing human workers, cobots augment their capabilities, doing heavy and repetitive tasks while humans focus on more complex tasks. As a result, workers experience enhanced job satisfaction and morale.
Improved Sustainability: Cobots can be more energy-efficient than traditional machinery, contributing to sustainability goals.
This cobot sets in the middle of the shop flood. There is no need to isolate them since they have safety features that allow them to operate among human workers.
Cobots are a valuable addition to the packaging and palletizing industry, offering myriad advantages in productivity, cost-efficiency, safety, and more.
How do the leading corporations use cobots to improve packaging and palletizing?
Among the vanguard of industries implementing collaborative robots are four pioneering companies: Amazon, Coca-Cola, Procter & Gamble, and DHL. Here is how cobots help them in their manufacturing operations:
Amazon: The retail giant utilizes cobots in its warehouses for packaging and palletizing. Robots assist human workers by transporting items, reducing the physical strain on employees and increasing efficiency.
Coca-Cola: The beverage company uses cobots in their production lines for packaging. The robots are programmed to handle different package sizes, ensuring a more flexible and scalable operation.
Procter & Gamble: The multinational manufacturer employs cobots to handle products of different shapes and sizes, improving packaging efficiency and accuracy.
DHL: DHL uses cobots for palletizing parcels in their delivery and logistics operations, allowing quicker sorting, dispatching, and boosting productivity.
Wrapping up
Integrating cobots into packaging and palletizing operations marks a significant modernization in industrial automation. These collaborative robots are not only redefining efficiency and accuracy, but they are also ensuring a safer and more harmonious working environment. As cobots develop and become more sophisticated, their impact on the packaging and palletizing sectors will undeniably grow, paving the way for a more innovative and productive future.