Europe is on the cusp of introducing virtual factories as a means to drive the next industrial revolution. With the aim of enhancing competitiveness in global markets, a research project funded by the EU is exploring the use of "digital twins" to create virtual factories that streamline production processes.
By leveraging technologies such as cloud computing, artificial intelligence, robotics, and blockchain, manufacturers can develop models of entire manufacturing processes and identify areas for improvement.
Digital twins are virtual representations of physical objects, processes, or systems. They are created using real-time data from sensors, Internet of Things (IoT) devices, and other sources to capture the behavior, characteristics, and performance of their real-world counterparts.
Essentially, a digital twin is a digital replica that mirrors the physical entity in a virtual environment.
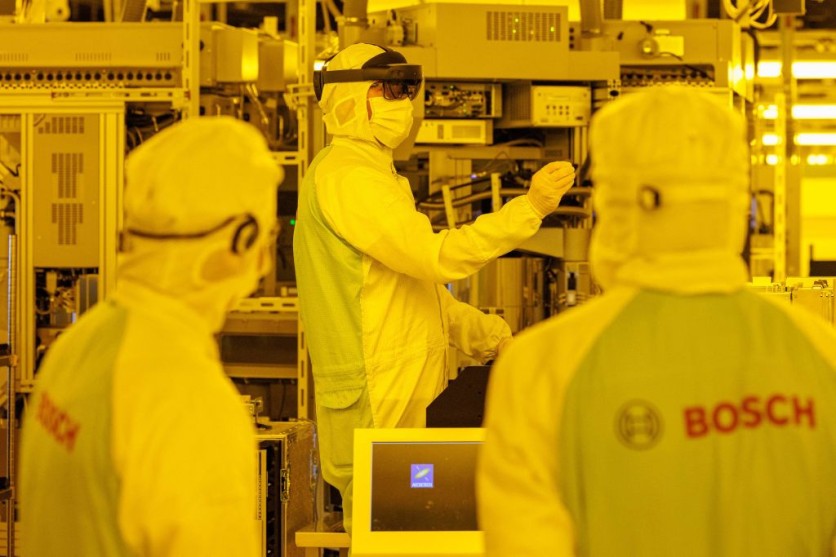
"Plug and Produce"
According to a report from Horizon: The EU Research & Innovation Magazine, the initiative known as DIMOFAC, which runs until March 2024, is at the forefront of this effort. The project has developed the "Plug and Produce" system, which facilitates easier reconfiguration of production lines by linking real machines with their digital counterparts.
Manufacturers can simulate new setups virtually, identifying and resolving any issues before implementing them in physical factories. This approach aims to reduce reconfiguration times and improve agility in manufacturing.
DIMOFAC will test the "Plug and Produce" system in five production facilities across Europe. These include the production of electric shavers in the Netherlands, aerospace components in Ireland, and interactive displays in Switzerland.
The results of the testing phase are expected to be available in the first quarter of 2024.
Read Also : EU's Digital Services Act Names Tech Companies That Must Follow its Latest Rules; Violators To Be Fined
FIRST Project
The EU-funded project, FIRST, focused on advancing the concept of digital factories to enhance efficiency across multiple production sites. By developing new designs and processes, FIRST aimed to promote collaboration among different manufacturing locations.
Through the use of information technology networks, blockchain, and virtual models, companies could coordinate global manufacturing and sales, resulting in more streamlined and environmentally friendly processes.
Virtual-factory technologies offer manufacturers the flexibility to adopt specific components and processes without the need for a complete system overhaul.
This is especially advantageous for small and medium-sized enterprises within Europe's manufacturing sector, as it enables them to improve their processes and reduce costs associated with machine maintenance.
The potential of virtual factories has prompted the FIRST consortium to actively seek additional funding to further advance these technologies. With Europe's manufacturing sector facing global competition and evolving environmental regulations, virtual factories hold promise for revolutionizing the industry and driving growth in the region.
Related Article : EU Official Urges Elon Musk to Make Progress on Twitter Amid New Law Against Hate Speech, Misinformation
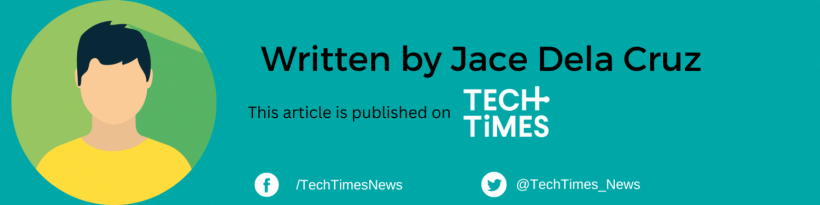
ⓒ 2025 TECHTIMES.com All rights reserved. Do not reproduce without permission.