Researchers have made a significant advancement in 3D printing technology by developing a highly electrically conductive metallic gel.
It allows for the creation of three-dimensional solid objects at room temperature, revolutionizing the manufacturing industry and paving the way for a wide range of electronic components and devices.
3D Printing Gel
The process begins with a solution containing micron-scale copper particles suspended in water. A small amount of indium-gallium alloy, which remains in a liquid state at room temperature, is added to achieve the desired properties. The mixture is then stirred, causing the liquid metal and copper particles to bind, forming a metallic gel network within the solution.
The gel's gel-like consistency is crucial as it ensures a uniform distribution of copper particles, allowing for the formation of electrical pathways. Moreover, this consistency prevents the copper particles from settling and obstructing the 3D printer nozzle.
"This gel-like consistency is important because it means you have a fairly uniform distribution of copper particles throughout the material," said Michael Dickey, co-corresponding author of the study and Camille & Henry Dreyfus professor of Chemical and Biomolecular Engineering at North Carolina State University.
"This does two things. First, it means the network of particles connect to form electrical pathways. And second, it means that the copper particles aren't settling out of solution and clogging the printer," Dickey added.
The gel obtained from the process can be easily printed using a conventional 3D printing nozzle, retaining its shape throughout the printing process. As the printed object dries at room temperature, it becomes even more solid while preserving its original form.
Intriguing Aspect
However, the introduction of heat during drying introduces an intriguing aspect. The arrangement of particles influences the drying process, resulting in structural modifications within the printed object.
For instance, applying heat causes greater contraction of the sides compared to the top and bottom in the case of a cylindrical object. By carefully manipulating the pattern of the printed object and adjusting the amount of heat applied, users can deliberately modify the object's shape after it has been printed.
Aside from its shape-shifting capabilities, the metallic gel boasts exceptional conductivity. As the printed objects consist of up to 97.5% metal, they exhibit high conductivity levels, albeit lower than conventional copper wire, according to Dickey.
The researchers are enthusiastic about the numerous applications of this technology. While it may not replace the traditional copper wire, the conductivity of the printed objects opens up a realm of possibilities for various industries.
The team welcomes collaboration with industry partners to explore potential applications and is eager to discuss future research directions with potential collaborators. The findings of the study were published in the journal Matter.
Related Article : World's First Non-Toxic Water-Based Aluminum-Ion Batteries Successfully Developed by Chinese, Australian Scientists
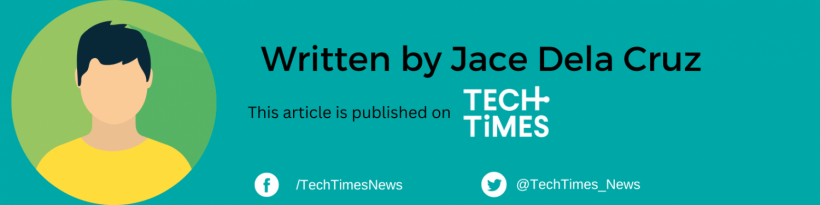