The University of Michigan researchers have developed a method for creating ultra-lightweight, waste-free concrete using 3D printing technology called the "Shell Wall."
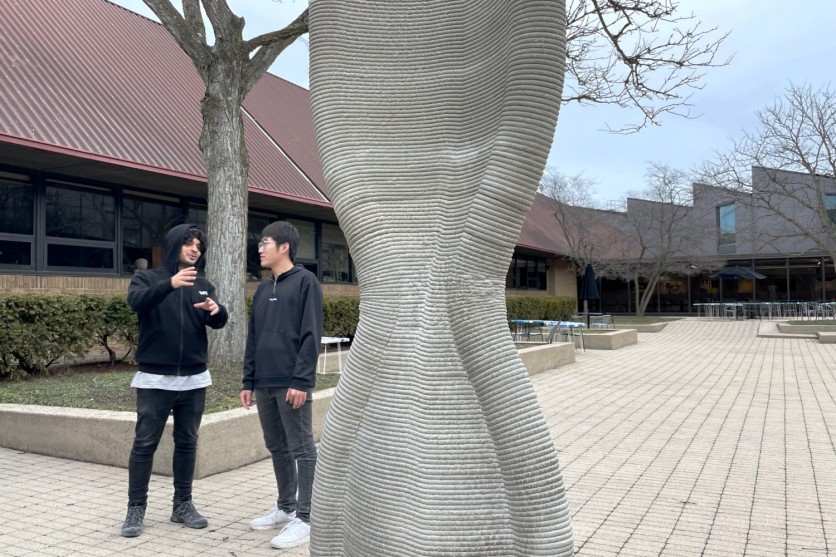
3D Concrete Printing
Architect Mania Aghaei Meibodi and researchers Alireza Bayramvand and Yuxin Lin of the DART lab at U-M's Taubman College of Architecture and Urban Planning combined topology optimization with 3D concrete printing to develop a computational model that synergizes nonplanar and variable material deposition based on the shape and geometric features of the topology-optimized parts.
This reduces weight by 72% compared to conventional, solid concrete of the same size and eliminates unnecessary overbuilding with excessive materials.
"This leads to high concrete consumption and limits its application for lightweight forms that entail intricate shapes like branching and angular tubular forms, overhangs, layer cantilevers, and filament section or angle variations," Aghaei Meibodi, assistant professor of architecture at Taubman College, said in a press release statement.
The researchers' approach shows promise for the construction industry, which is beginning to embrace 3D printing as a promising tool for innovation and sustainability.
The method allows for efficient use of material by placing it precisely where needed for structural purposes, leading to better and more environmentally friendly structures at a lower cost.
The most popular method for 3D concrete printing on building sites use a planer toolpath; due to geometric restrictions, it can only be applied to simple structures like orthogonal walls.
This is the path that the tool head takes as it pushes mortar out of the printing head and deposits it in horizontal layers. The deposited layer's height elevates the extruder nozzle following each layer's deposit.
Repeating this procedure results in a concrete mold loaded with rebars and concrete.
Nonplanar 3D Printing
Nonplanar 3D printing has been investigated in the past for complex geometries, but little emphasis has been paid to employing concrete, according to Bayramvand and Lin.
The Peri Group, ICON, and WASP, three well-known pioneers in 3D concrete construction, are starting to take notice of these technological developments from the DART Lab researchers.
The building industry is embracing 3D printing as a promising tool for innovation and sustainability.
The U-M team's innovative strategy creates new partnerships intended to enhance future outcomes for legislators, 3D concrete printing businesses, and the overall concrete sector.
With rapid urbanization and increased demands to build infrastructure, their work may contribute to significant changes in the construction industry and general 3D concrete printing practices.
Related Article : Lockheed Martin Partners With 3D Printing Company for Research Expansion of Metal Additive Parts
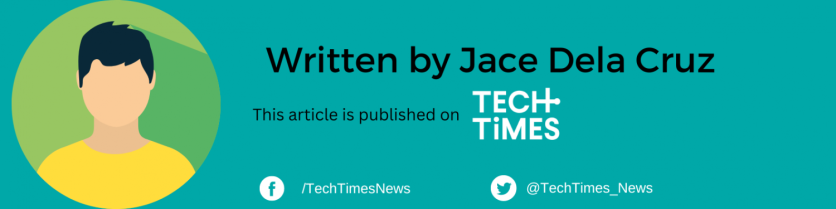
ⓒ 2025 TECHTIMES.com All rights reserved. Do not reproduce without permission.