Texas will soon be home to the world's first 3D-printed hotel, thanks to a collaboration between hospitality entrepreneur Liz Lambert, and construction startup Icon, and Danish design firm BIG, as reported first by Interesting Engineering on Friday, March 25.
Located in the town of Marfa, the hotel is expected to open in 2023, and it will feature unique accommodations built using innovative 3D printing technology.
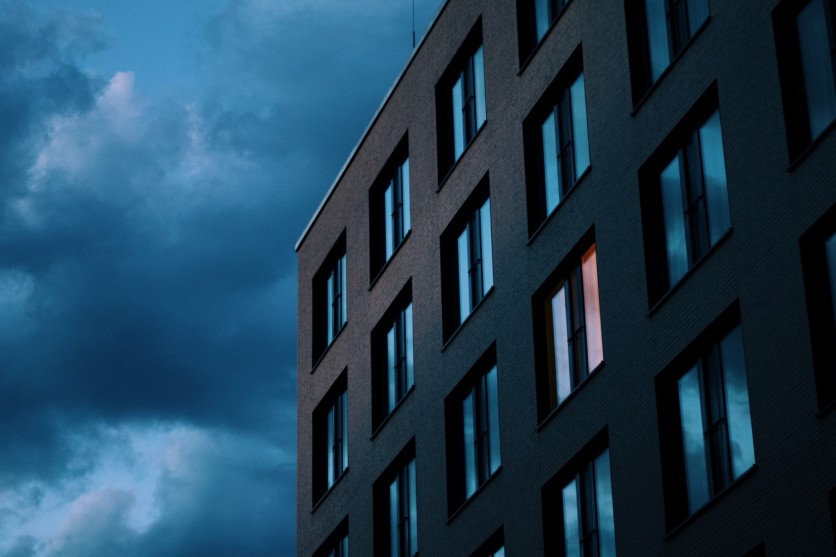
Triple the Size of El Cosmico
BIG is no stranger to innovative architecture, having designed renowned structures such as the VM Houses and Mountain Dwellings in Copenhagen.
Now, the firm is teaming up with Lambert and Icon to create something that has never been done before. The new hotel will be built on the same site as Lambert's existing El Cosmico camping site, which is already a must-visit destination for travelers from around the world.
Once complete, the 3D-printed hotel will nearly triple the size of El Cosmico, expanding from 21 to 62 acres. The hotel will feature a range of amenities, including a massive infinity pool with cabanas, unique guest dwellings, and other elements that are sure to make a summer vacation unforgettable.
The hotel's unique guest accommodations will be built using Icon's efficient home-sized 3D printer, the Vulcan. The printer will be paired with Icon's portable mixing unit, called Magma, which produces the building material known as Lavacrete.
Developed by Icon's material science team, Lavacrete is a sturdy, reliable substance that has been thoroughly tested to ensure it can withstand the test of time.
Read Also : Lockheed Martin Partners With 3D Printing Company for Research Expansion of Metal Additive Parts
Large-scale 3D Metal Printing
In related news, Rosotics, an Arizona-based company, has announced the launch of its revolutionary "rapid induction printing" technology, which aims to transform large-scale 3D metal printing.
The approach was developed by Rosotics' founder and CEO, Christian LaRosa, and it has the potential to dramatically reduce costs and improve safety and energy efficiency.
Traditional additive metal manufacturing involves using lasers to heat and melt powdered metal feedstocks, a process that can be both expensive and hazardous.
Rosotics' approach, on the other hand, uses induction to heat metal inductively, a natural and highly efficient way to 3D print metal.
The company's new printing head, called Mantis, delivers heat to the metal inductively, which speeds up the printing process while reducing costs. The printer can create parts that are big enough for structural use in aircraft and rockets, making it an attractive option for industries that require large-scale metal parts.
Another advantage of Rosotics' approach is that it can use a wide range of metals, as the feedstock does not have to be ferromagnetic. The printer can handle wires between 1-10mm in diameter, which can be scaled up if necessary.
With the launch of this new technology, Rosotics is poised to revolutionize large-scale 3D metal printing, making it more accessible, efficient, and cost-effective than ever before.
Read also: 'Chameleon Robots:' These Robots Can Change Colors and Mimic Their Surroundings Through 3D Printing
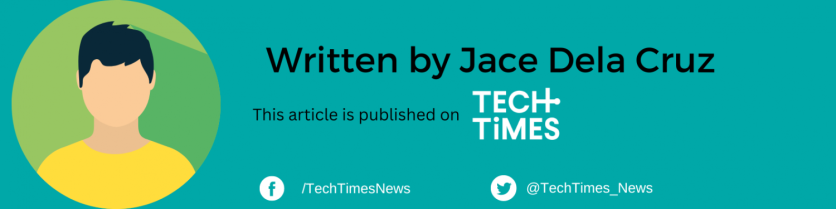
ⓒ 2025 TECHTIMES.com All rights reserved. Do not reproduce without permission.