Researchers from the Sandia National Laboratories want to join the global effort of reducing greenhouse gas emissions through 3D printing. They have demonstrated that a novel 3D-printed superalloy could boost power plants into producing more electricity with less carbon.
High-performance Metal Alloy
Sandia scientists worked with researchers from Iowa State University, Bruker Corp., and Ames National Laboratory to 3D print a high-performance metal alloy or superalloy.
According to the research team, this superalloy has a unique composition making it lighter and stronger than current cutting-edge materials used in gas turbine machinery.
The findings suggest a new class of undiscovered alloys that could have extensive applications for the energy sector and the aerospace and automobile industries.
Sandia scientist Andrew Kustas claims that this novel material can access unprecedented combinations of high-temperature resiliency, high strength, and low weight with the help of the additive manufacturing approach.
The new superalloy is 42% aluminum, 25% titanium, 13% niobium, 8% zirconium, 8% molybdenum, and 4% tantalum. The team's experiments demonstrated that it was stronger at 800 degrees Celsius (1,472 degrees Fahrenheit) compared to other superalloys, and it remained stronger even after being cooled down to room temperature.
"This is therefore a win-win for more economical energy and for the environment," Sal said in a press release statement.
The discoveries may be useful for more than just the energy sector since lightweight materials that maintain strength under extreme heat is also sought after by aerospace experts.
Ames and Sandia are also collaborating with businesses to investigate how alloys like these could be employed in the automobile sector, according to Nic Argibay, an Ames Lab scientist.
Read Also : Lockheed Martin Partners With 3D Printing Company for Research Expansion of Metal Additive Parts
Additive Manufacturing
The manufacturing process known as additive manufacturing or 3D printing is renowned for being adaptable and low-energy. A high-powered laser is frequently used in printing to quickly melt a substance, typically plastic or metal. Once the molten material rapidly cools and hardens, the printer deposits the material in layers, creating an item.
This new study shows how 3D printing may also be used to create new materials quickly and effectively. Members of the Sandia team used a 3D printer to swiftly fuse metal powders and create a sample out of it.
Sandia's invention also signifies a fundamental shift in the way alloys have been created because no single metal comprises more than half of the material. Steel, on the other hand, consists primarily of iron-nearly 98% of it-mixed with carbon and other materials.
The team is now interested in investigating if cutting-edge computer modeling approaches could aid in the discovery of more members of what may turn out to be a new class of superalloys that are suited for additive manufacturing.
The study was supported by the Department of Energy and Sandia's Laboratory Directed Research and Development program.
The research team's findings were published in the journal Applied Materials Today.
Related Article : 'Chameleon Robots:' These Robots Can Change Colors and Mimic Their Surroundings Through 3D Printing
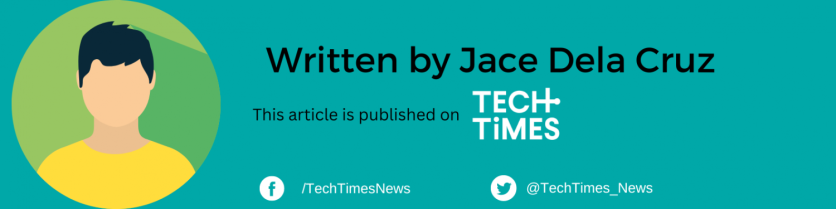
ⓒ 2025 TECHTIMES.com All rights reserved. Do not reproduce without permission.