Rope Robotics, a producer of robotic blade maintenance technology from Denmark, has recently begun testing its robots on offshore wind turbines in hopes of making them commercially available in 2023.
However, the company is also making sure that they have the most advanced robots as it plans to integrate artificial intelligence into them, according to a report by offshoreWIND.biz.
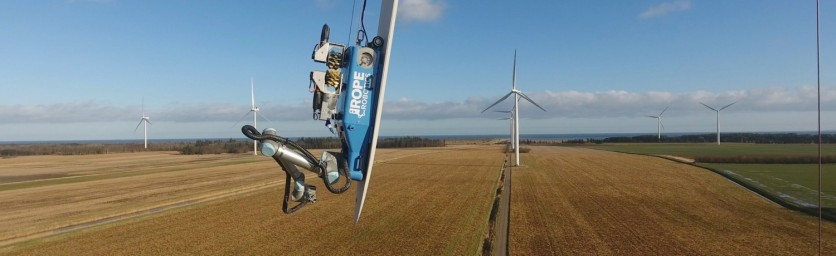
Blade Maintenance Robot
According to the company, nine BR-8 robots are currently in commercial use on several wind farms across Europe, Canada, South Africa, and the US. The robots have fixed more than 150 onshore wind turbine blades that had been damaged by rain over the past 18 months.
Rope Robotics claims that its BR-8 can recover up to 3% of energy output per blade in less than a day, which is also half the cost of current manual solutions.
According to the company's CEO, Martin Huus Bjerge, client feedback has been largely positive, especially in the US and South Africa.
The company's press release on Feb 6 indicates that test repairs on offshore wind turbines are currently being carried out. By the end of 2023, Rope Robotics intends to introduce its robots for commercial use in the offshore wind sector.
The company is also investing in AI so that it can equip autonomy on its repairing robots in the future.
Read Also : China's New 18-MW Model Steals 'World's Largest Offshore Wind Turbine' Title from Previous 16 MW
How Does the Robot Function?
The blade maintenance robot has a flexible arm to control repair tools and visual sensors. They are also remotely controlled by technicians via on-screen live images that are, in turn, used for documentation purposes.
The 150-kg robot is raised approximately 100 meters above the ground by ropes connected in the nacelle after the damaged blade has been placed in a vertical position.
The robot can firmly cling to the blade with the help of a vacuum system, and it can travel across it with the use of motors.
The robot scans the surface with its integrated high-resolution camera and laser scanner, providing images to the remote operator, who then assesses the damage and starts the repair procedure in real time, according to Rope Robotics.
The repair process is divided into three steps: sanding the damaged area comes first, then a second tell cleans the surface off of grease and dirt.
Lastly, a spreading tool renews the optimal aerodynamic blade form, while a closing tool applies the leading-edge protection (LEP) material to smooth the fabric to predefined requirements.
The Danish Government's Scheme for Energy Technology Development and Demonstration Program (EUDP) awarded DKK 16 million ($2.5 million) to Rope Robotics in 2018 to advance their technology.
The company took five years to develop the process and the spreading tool. The robot was only unveiled to the public by 2021, following five years of developing the repairing strategy and the spreading mechanism. Rope Robotics currently holds two patents on the robot system and is well on its way to commercial production in 2024.
Related Article : Scientists Create An 'Odd Material' for Wind Turbines That Can Be Recycled Into Gummy Bears - How?
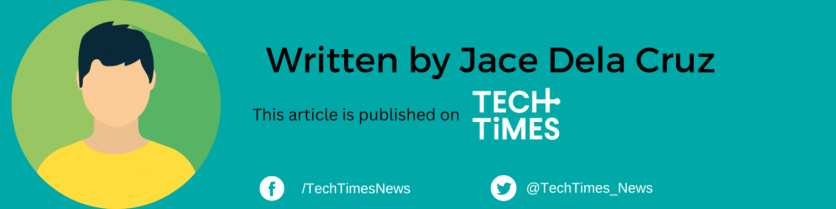