Recycling batteries would significantly reduce reliance on these materials, boost supply chain safety, and lessen the human and environmental impact that comes with using batteries. BASF, a chemical giant, aims to build a battery-recycling factory utilizing black matter to meet this goal.
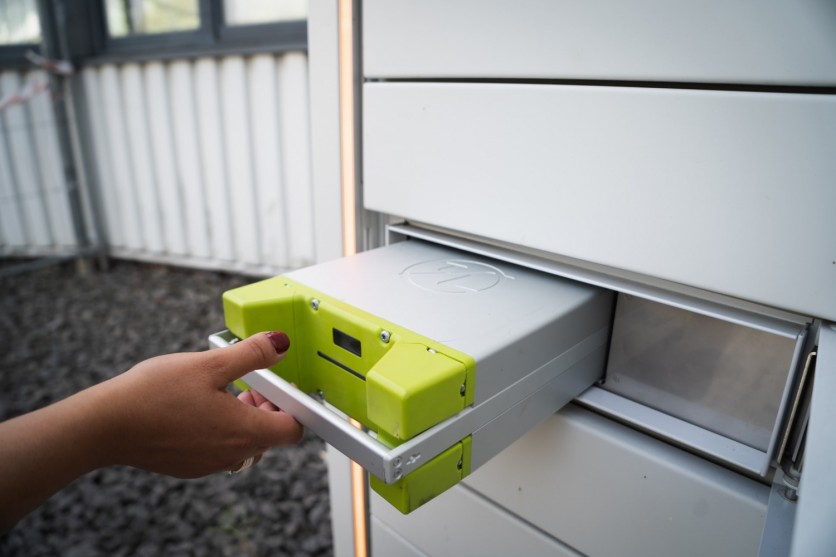
Are Batteries Really Recycled?
Batteries like lithium are really recycled through huge factories in the process of shredding them down into a powder. This powder is then either melted, or what we call pyrometallurgy, or dissolved in acid, also known as hydrometallurgy. This allows its component elements to be extracted for resale. This strategy has been used by several enterprises and plant giants.
As an example, a report from Tech Times shows that Norway just opened the same huge recycling plant known as Hydrovolt. Every year, it can process 12,000 tons of battery packs. This implies that the new batt recycling plant can house over 25,000 electric car batteries.
Also Read : Largest EU Battery Recycling Plant Enough for Norway's Batteries; 95% of Materials Can Be Recovered
BASF's Commercial Battery-Recycling Plant
According to Electrek, the global chemical company BASF plans to construct a commercial battery-recycling, black-mass factory in Schwarzheide, which is a town located in Brandenburg, eastern Germany.
The first phase in the battery recycling process is the manufacture of black mass, which comprises large levels of lithium, nickel, cobalt, and manganese - the main metals necessary to generate active cathode materials. As per BASF, the new factory would increase the production of active cathode materials, which is the core component of lithium-ion batteries. This plant will serve as a battery recycling hub in Schwarzheide.
It will handle 15,000 tons of electric car batteries and manufacturing scrap each year. It is planned to launch in early 2024, creating around 30 new manufacturing jobs.
The black mass will subsequently be sent to BASF's commercial hydrometallurgical refinery for battery recycling, which is expected to be completed in three years. BASF's catalysts division president, Dr. Peter Schuhmacher, stated that the company's investment in a commercial-scale, battery-recycling, black-mass factory is the next step in establishing the whole battery recycling value chain.
This enables them to optimize the entire recycling process and cut CO2 emissions.
Dr. Schuchmacher also added, "The closed loop from end-of-life batteries to [cathode active materials] for new batteries supports our customers along the entire battery value chain, reduces the dependency from mined raw materials, and enables a circular economy."
Because of the presence of several EV makers and cell producers in Central Europe, the business believes the location is suitable for expanding battery recycling activities.
Speaking of recycling EV batteries, bioleaching is another option in addition to hydrometallurgy. It entails the use of metal-oxidizing microorganisms as part of their metabolic activity.
An article from Tech Times suggested that bioleaching is currently being used to clean and recover materials from various electronic wastes. Given that EV batteries are still in their infancy, it would be an efficient method of recycling them.
Related Article : EV Batteries Can Be Recycled Using Bacteria - What You Need to Know About Bioleaching
This article is owned by Tech Times
Written by Thea Felicity
ⓒ 2025 TECHTIMES.com All rights reserved. Do not reproduce without permission.