NASA is recently exploring its joint venture in the high-technological capabilities of 3D printing specialization with the Aerojet Rocketdyne.
The collaboration is said to be made possible for the manufacturing of the metal additive rocket engine hardware, which will be used for the landers' liquid rocket engines as well as for the spacecraft.
NASA Joins RDT Project Team for Automated Robotic Deposition Processes
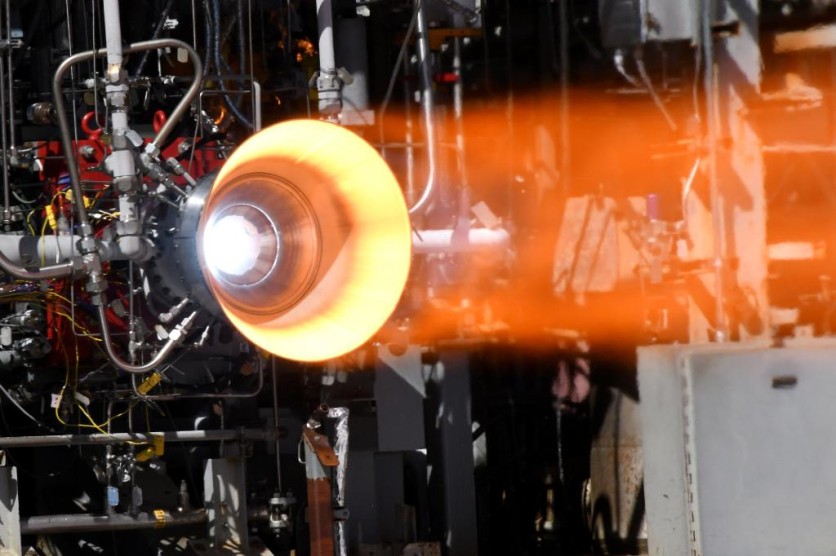
According to a NASA report which was updated on Monday, May 17, the Huntsville, Alabama-based Marshall Space Flight Center of NASA has connected to the Robotic Deposition Technology (RDT) team for the design and creation of the metal additive 3D-printing technology.
The assigned crew in the project has taken over the task of the innovative manufacturing of the lightweight combustion injectors, nozzles, and chambers which will be integrated into the 3D-printing's automated robotic deposition.
The processes involved in this test are the laser wire direct closeout, cold spray deposition, laser powder directed energy deposition, and laser powder bed fusion.
According to the people responsible for these processes, the evolution of these procedures remains the goal through the help of the weight-optimized materials via hot fire testing. This will further validate and evaluate the performance, usability, and operability of the lightweight materials.
LLAMA Project Underscores Hot Fire Testing of the RDT Project Team
The above-mentioned hot fire test for the lightweight combustion nozzle and chamber, as well as the carbon composite nozzles and injectors, have successfully undergone the Long Life Additive Manufacturing Assembly (LLAMA) project test.
According to the Marshall engineer, Thomas W. Teasley, there is a good result for the latest RDT Advanced Lander Propulsion Additive Cold-spray Assembly (ALPACA) chamber test. Additionally, they also managed to make a newly-capable technology for NASA and its partners.
"The RDT ALPACA effort between NASA and Aerojet Rocketdyne is another example of our collaboration and partnership in advancing additive manufacturing technologies," Bryan Webb, a senior engineer of the Aerojet Rocketdyne said.
For those who have little idea about the Aerojet Rocketdyne, it was also one of the contributors to why the NASA Perseverance rover landing was successful. Global Newswire reported that its propulsion had become a critical component of NASA's 9th Mars touchdown.
For the total hot fire duration of the hardware, there are eight reported starts at 365.4 seconds. For the main combustion chamber, all the examinations done have produced up to 750 psi (pound-force per square inch) in addition to the 6,200 degrees Fahrenheit calculated as the hot gas temperatures.
The 7,00-pound thrust for three various carbon composite nozzles has been tested in extreme conditions which exceeded over 4,000 degrees Fahrenheit of temperature.
In the long run, we could surmise that the advancements handled by the RDT will aid NASA in general. It has paved the way for the production of the more efficient liquid rocket engine components compared to their traditional counterpart which is outdated, more costly, and heavier due to the required multiple parts.
Related Article: NASA's New Space Lasers Offers 10x to 100x Faster Data Transmission: LCRD's Details
This article is owned by Tech Times
Written by Joseph Henry
ⓒ 2025 TECHTIMES.com All rights reserved. Do not reproduce without permission.