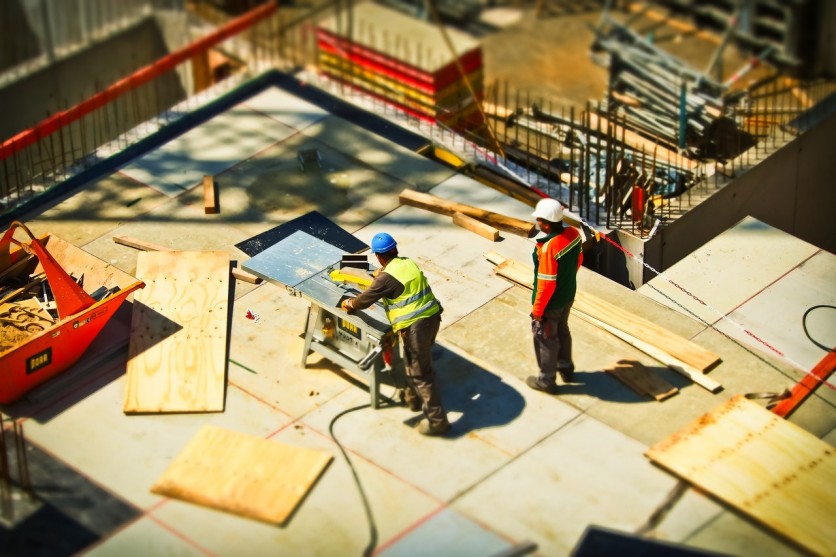
Composite materials have come a long way since they first appeared on the market. Back then, they were not as versatile, durable, and aesthetically pleasing as the ones we use today. Today, composite decking manufacturers employ techniques that improve composites even further. What are these practices, and how does it affect the overall quality of composites?
Producing Composite Materials
There are various ways of producing composite materials. The most popular method is through moulding. Moulding composites have two types of categories; open and closed moulding.
Open moulding involves extruding thermoplastic resin into wood fibres and placed in an open mould. The process is relatively cheaper and better suited for low-volume productions. On the other hand, closed moulding uses two-sided, sealed moulds. In terms of consistency, precision, and waste production, closed moulding is better. However, it can be more expensive than open moulding.
Both open moulding and closed moulding have different sub-categories. Each process has its advantages and disadvantages. For open moulding, hand layup and filament winding are a few examples of more commonly-used processes. As for closed moulding, pultrusion, vacuum infusion, and compression moulding are the most widely-used methods.
Composite Capping
Once moulded and produced, composite decking materials are ready for construction projects. However, using them presents a few problems. The older generations of composites are more susceptible to wet environments, thermal expansion, and other issues.
To further the quality of wood-plastic composites, many manufacturers decided to add another layer of protection around the material. Because of this, most composites in the market today have capping. Manufacturers bind thermoplastics, such as HDPE and PVC, as an outer protective coating to the composites. The capping material also affects the boards' slip, moisture, and fade resistance.
How manufacturers use capping techniques vary. For instance, UltraDecking, a reliable composite decking supplier in the UK, offers various products with different caps. Their composite decking boards have three-sided capping, ranging from platinum top caps to standard. Their finest products offer superior slip, stain, and scratch resistance as well.
Increasing Moisture Resistance
Despite what some may believe, composite materials still absorb some moisture. While not nearly comparable to wood's absorption rate, it can still pose some problems. Because of this, many manufacturers looked for ways to prevent and minimize moisture by increasing the board's density.
Many composite manufacturers used various fillers, cellulose fibres, and additives to produce a denser, more water-proof composite material. Some companies also see the potential use of Antioxidants. Antioxidants can decrease the rate of degradation, which occurs in synthetic materials over time. As a result, it also slows down the decrease of density in plastic and composite decking materials.
Better Sustainability
Composite materials are the answer to the ever-increasing need for wood. While wood is a natural and safe resource, the high demand for lumber materials can harm the environment. As more people want lumber, over-harvesting trees lead to deforestation.
Composites before are not as sustainable as the ones used today. But now, more manufacturers are helping the environment by finding greener options in composite production. For instance, many brands have composite decking boards that use recycled plastic bottles and bags that would have ended up in landfills. Many also reuse industrial wood waste such as wood chips and wood flour from wood processing plants.
Today, composites are greener than ever. Not only do they use recycled materials, but they also don't need maintenance treatments. You don't need to apply stains, paints, and seals containing chemicals harmful to the environment.
Hollowed Decking Boards
An advantage of synthetic products is the manufacturers having the ability to shape them according to need. As for composites, many manufacturers produce composites with hollowed centres, which significantly improves their performance in some aspects.
Hollowed decking boards solved several problems with decking. Because fewer materials are needed to produce them, they are significantly less expensive than solid decking boards. It also has a lesser impact on the environment than creating solid decking boards.
Hollowed decking boards are also lighter than traditional decking boards. This improvement is beneficial for DIY builders, as they won't require as much assistance in transporting and installing these decking boards. They also don't necessarily need sturdier frames, which require using more pressure-treated lumber.
In conclusion, there are many processes and techniques used today to improve composite decking materials. Many companies, manufacturers, and suppliers take advantage of these advancements. Moving forward, we can expect more changes in composite materials in the future.