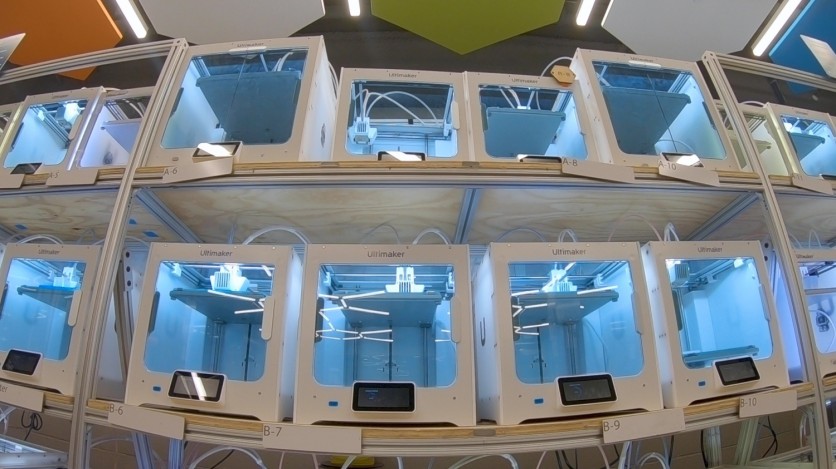
A Duke University task force has been working tirelessly to assure and protect Duke Health from experiencing a shortage in medical equipment and supplies. As frontliners work to give patient care during the ongoing COVID-19 pandemic, the University has taken the challenge of creating face shields using 3D printing technology.
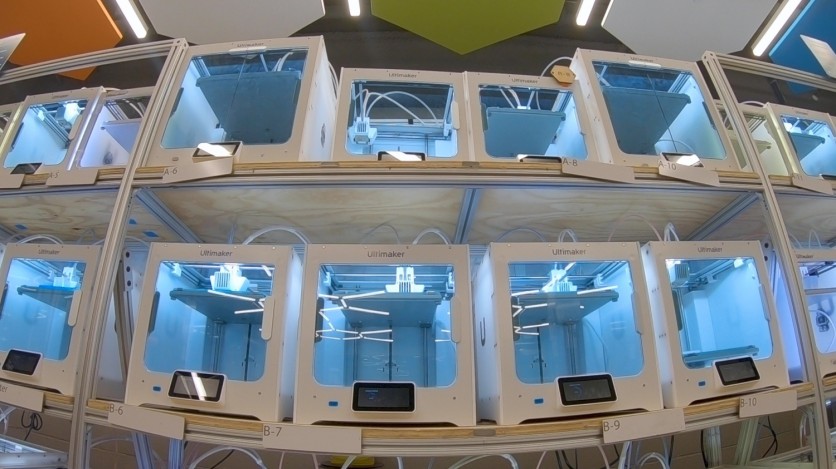
Read Also : Scientists Have Identified the 'Achilles Heel' of the Coronavirus that Can Potentially Lead to a Vaccine
Reusable face shields have been developed using Duke's 3D printing technology
Duke engineering professors Ken Gall, Eric Richardson, and Paul Ferris were thinking of ways on how to address the medical supply shortage that many healthcare institutions have been experiencing because of the ongoing COVID-19 pandemic.
Colleagues from the Pratt School of Engineering's Engineering Entrepreneurship (EngEn) team and several fellows in Richardson's Duke Design Health course were assigned to look into designs for different kinds of medical devices that they could produce. The project also attracted students from Duke's School of Medicine, Duke Engineering, Fuqua, and Trinity as well as Nursing.
Equipped with more than five dozen 3D printers, Duke's Innovation Co-Lab in the Office of Information Technology developed a plan to use their state-of-the-art 3D printing lab to design and produce supplies.
The lead role in exploring and identifying the best case on where to use their technology was taken by Co-Lab's Sr. Engineer and Fabrication Architect, Chip Bobbert. He then acted quickly and created a design task force which consists of 15 people.
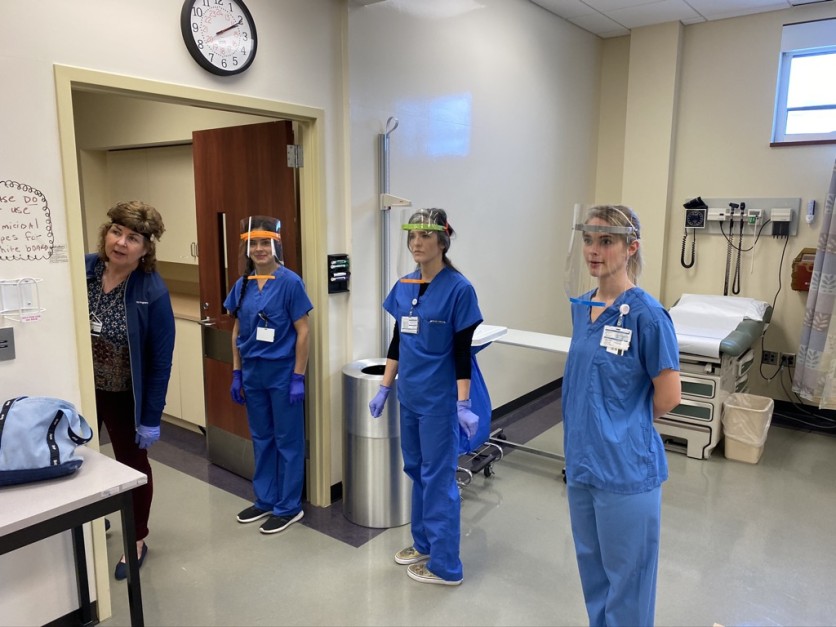
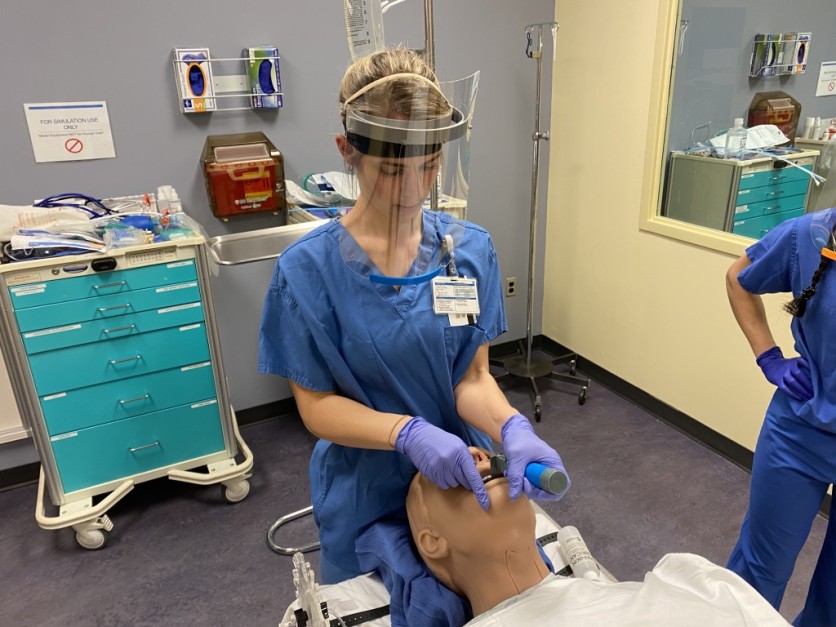
Coordinating with on which equipment is needed the most
Richardson said that "Duke is a special place where we can bring together several departments quickly and leverage relationships that already exist. The collaborative nature of Duke has been critical to our success."
As the need for more medical supplies grows each day, Duke Engineering, Duke Health and OIT teams were more careful and analytical with their approach. They began coordinating with various health care workers and tried to assess and determine their priorities in terms of equipment.
It became obvious that reusable medical face shields were more helpful; they began to do tests, printing different kinds of prototypes.
After about a week of print testing at least 100 designs, the task force settled on a particular one which is the prototype of a 3D printed headband that molds and forms into a face shield when latched to a laser-cut polycarbonate lens. The lens is lightweight with high-impact resistance and is made of plastic.
The executive director of Duke MEDx, Donna Crenshaw, said that these newly developed 3D face shields will serve as added protection from contamination and, at the same time, will also help save the finite resource of N95 respirator masks.
"It is an extra level of safety for the person who is dealing with a COVID patient or somebody who may have COVID, so it's an extra barrier," Crenshaw added.
More than two dozen nurses at Duke, medical experts, and graduate nursing students tested these 3D printed face shields in a lab under simulation. The results revealed that they have met safety standards and can be reused after a thorough sanitizing process.
Duke has partnered with UNC-Chapel Hill in developing the face shields which will all be distributed at both UNC Health Systems and Duke.
ⓒ 2025 TECHTIMES.com All rights reserved. Do not reproduce without permission.