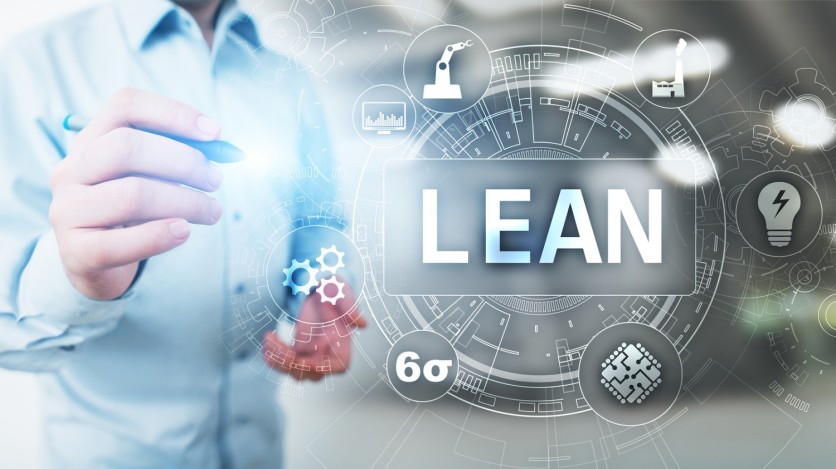
To improve the overall performance of your organization Six Sigma tools can be really helpful.
As the CEO of Global Six Sigma, Mr Peter Peterka puts it, "When developing a strategic plan, Six Sigma methodologies should be woven into every aspect of the plan for continuous improvement and success."
With the help of Six Sigma tools and techniques, you can not only fine-tune the various company processes but also empower your employees to perform better. The motto is to create a work process that contributes to more effective operations of the company as a whole.
Here are the 6 most effective Six Sigma tools that companies can adopt to attain continuous improvement in their processes.
1. The Five Whys
The root cause of a problem is possibly the most important thing that needs to be identified. The Five Whys exactly tries to attend to this issue. The root cause once identified helps in mitigating the problem with relative ease. Basically, the problem is further broken down using a series of Whys being asked to find out the root cause. This helps in faster problem resolution as the symptoms of a bigger problem doesn't take the centre stage thus saving vital time.
2. Poka-Yoke
This tool has a very simple logic behind its operation and that is the belief that multiple small adjustments and corrective measures can help in the resolution of a much bigger problem. Poka-Yoke works to reduce or better still eliminate all mistakes by humans in a process. The goal of the process is to ultimately have zero defects.
3. Control Charts
Control charts can be best described as analytical tools which can be used to understand and solve problems on smaller to very big scales. Control charts are basically a data reserve that has all the necessary inputs and metrics of a process which has undergone some procedural changes. The Control charts can map the various stages of a process which were undertaken before the changes were made and yet again a new set of Control charts can analyze the same stages of the process after the changes were made. Data is taken into consideration for a process on its key characteristics and outcomes.
4. Value Stream Mapping
this tool is excellent for addressing, identifying and eliminating waste along the entire cycle of a process. When a product is being developed, during the various steps of production, certain amounts of wastage are found to be present. The entire operational stages are scrutinized and mapped to accurately determine the extent of wastage and how it can be reduced. So, this Six Sigma process looks into finding what value each step brings in to the entire process. Once the mapping is done then the need for any adjustment is looked into for each step. The value stream mapping can identify the eight forms of waste which are defects, overproduction, waiting, non-utilized talent, transportation, inventory, motion and extra processing.
5. Fishbone Diagram
If you are looking for an effective graphical tool then this is the one for you. The root causes of the problems are determined in an organized way. This way when you'll look into the problems you'll find out ways to solve them efficiently. These graphical representations of problems will enable you to brainstorm in a more focused manner. Suppose you are noticing that stakeholders are not turning up in the meetings properly, you will find out the causes why... maybe the list that you are following for email distribution is pretty old. May be conflicting meeting is the case, etc. So, for a more focused solution, this tool is used. This is also called cause and effect diagram.
6. Takt Time
This tool is specifically used to meet client deadlines. With the help of this one, the production rhythm is maintained. The demand of the product or service among consumers is understood first and then the amount of time required delivering the service or the product to the customer is determined which is possible only after you've determined the demand first. This way not too much product is produced which helps in cutting down of superfluous production which is why a lot of time and money is saved.
ⓒ 2025 TECHTIMES.com All rights reserved. Do not reproduce without permission.